ปัจจัยต่าง ๆ ตั้งแต่รูปทรงเรขาคณิตและขนาดของชิ้นส่วนที่ถูกตัดเฉือนไปยังวัสดุของชิ้นงานต้องได้รับการพิจารณาเมื่อเลือกสิทธิ์เครื่องตัดสำหรับงานการตัดเฉือน
การกัดใบหน้าด้วยคัตเตอร์ไหล่ 90 °เป็นเรื่องธรรมดาในร้านขายเครื่องจักร ในบางกรณีตัวเลือกนี้เป็นธรรม หากชิ้นงานที่จะบดมีรูปร่างผิดปกติหรือพื้นผิวของการหล่อจะทำให้เกิดความลึกของการตัดที่แตกต่างกันโรงสีไหล่อาจเป็นตัวเลือกที่ดีที่สุด แต่ในกรณีอื่น ๆ อาจเป็นประโยชน์มากกว่าในการเลือกโรงสีใบหน้า 45 °มาตรฐาน
เมื่อมุมที่พรวดพราดของเครื่องตัดน้อยกว่า 90 °ความหนาของชิปตามแนวแกนจะเล็กกว่าอัตราการป้อนของเครื่องตัดหม้อเนื่องจากการทำให้ผอมบางของชิปและมุมตัดที่ลดลงอย่างมากจะมีอิทธิพลอย่างมากต่อการป้อนอาหารต่อฟัน ในการกัดใบหน้าโรงสีใบหน้าที่มีมุมที่พุ่งสูงขึ้น 45 °ส่งผลให้ชิปทินเนอร์ เมื่อมุมกระโดดลดลงความหนาของชิปจะน้อยกว่าฟีดต่อฟันซึ่งจะเพิ่มอัตราการป้อนโดยปัจจัย 1.4 เท่า ในกรณีนี้หากมีการใช้โรงสีใบหน้าที่มีมุมการพุ่งพรวด 90 °ผลผลิตจะลดลง 40% เนื่องจากผลการทำให้ผอมบางชิปตามแนวแกนของโรงสีใบหน้า 45 °ไม่สามารถทำได้
อีกแง่มุมที่สำคัญในการเลือกเครื่องตัดสีมักถูกมองข้ามโดยผู้ใช้ - ขนาดของเครื่องตัด ร้านค้าหลายแห่งต้องเผชิญกับการกัดชิ้นส่วนขนาดใหญ่เช่นบล็อกเครื่องยนต์หรือโครงสร้างเครื่องบินโดยใช้เครื่องตัดขนาดเส้นผ่าศูนย์กลางขนาดเล็กซึ่งทำให้มีพื้นที่มากสำหรับการผลิตที่เพิ่มขึ้น เป็นการดีที่เครื่องตัดการกัดควรมี 70% ของตัดขอบที่เกี่ยวข้องกับการตัด ตัวอย่างเช่นเมื่อการกัดพื้นผิวหลายส่วนของส่วนใหญ่โรงสีใบหน้าที่มีเส้นผ่านศูนย์กลาง 50 มม. จะมีการตัดเพียง 35 มม. ลดผลผลิต การประหยัดเวลาการตัดเฉือนที่สำคัญสามารถทำได้หากใช้เครื่องตัดขนาดเส้นผ่าศูนย์กลางที่ใหญ่ขึ้น
อีกวิธีหนึ่งในการปรับปรุงการดำเนินงานการกัดคือการเพิ่มประสิทธิภาพกลยุทธ์การกัดของโรงสีใบหน้า เมื่อการเขียนโปรแกรมการกัดผู้ใช้ต้องพิจารณาก่อนว่าเครื่องมือจะพุ่งเข้าใส่ชิ้นงานอย่างไร บ่อยครั้งที่การกัดมีดเพียงแค่ตัดเข้าไปในชิ้นงานโดยตรง การตัดประเภทนี้มักจะมาพร้อมกับเสียงกระแทกจำนวนมากเพราะเมื่อเม็ดมีดออกจากการตัดชิปที่สร้างขึ้นโดยเครื่องตัดสีจะหนาที่สุด ผลกระทบสูงของการแทรกบนวัสดุชิ้นงานชิ้นงานมีแนวโน้มที่จะทำให้เกิดการสั่นสะเทือนและสร้างความเครียดแรงดึงที่ทำให้อายุการใช้งานสั้นลง
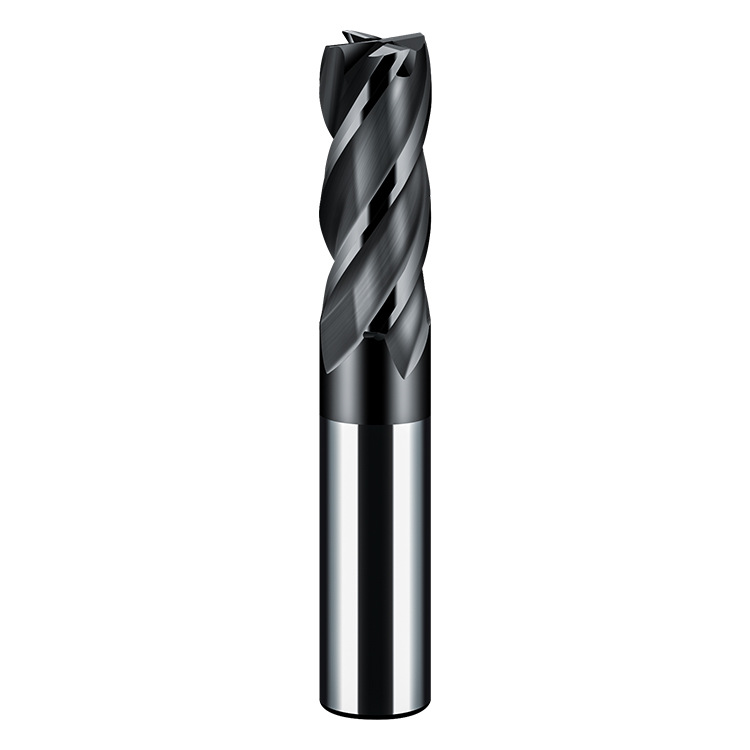
เวลาโพสต์: พฤษภาคม -12-2022