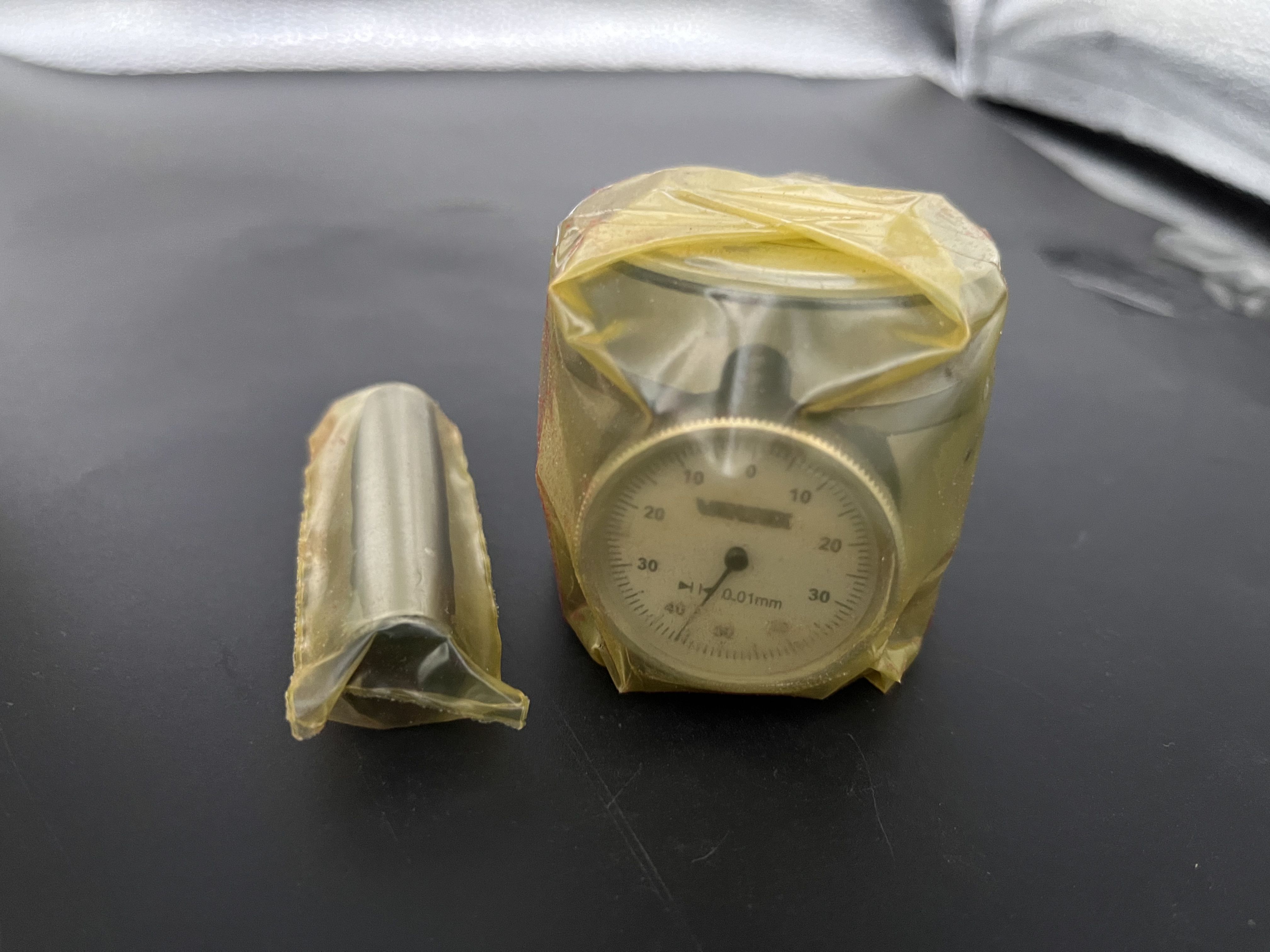
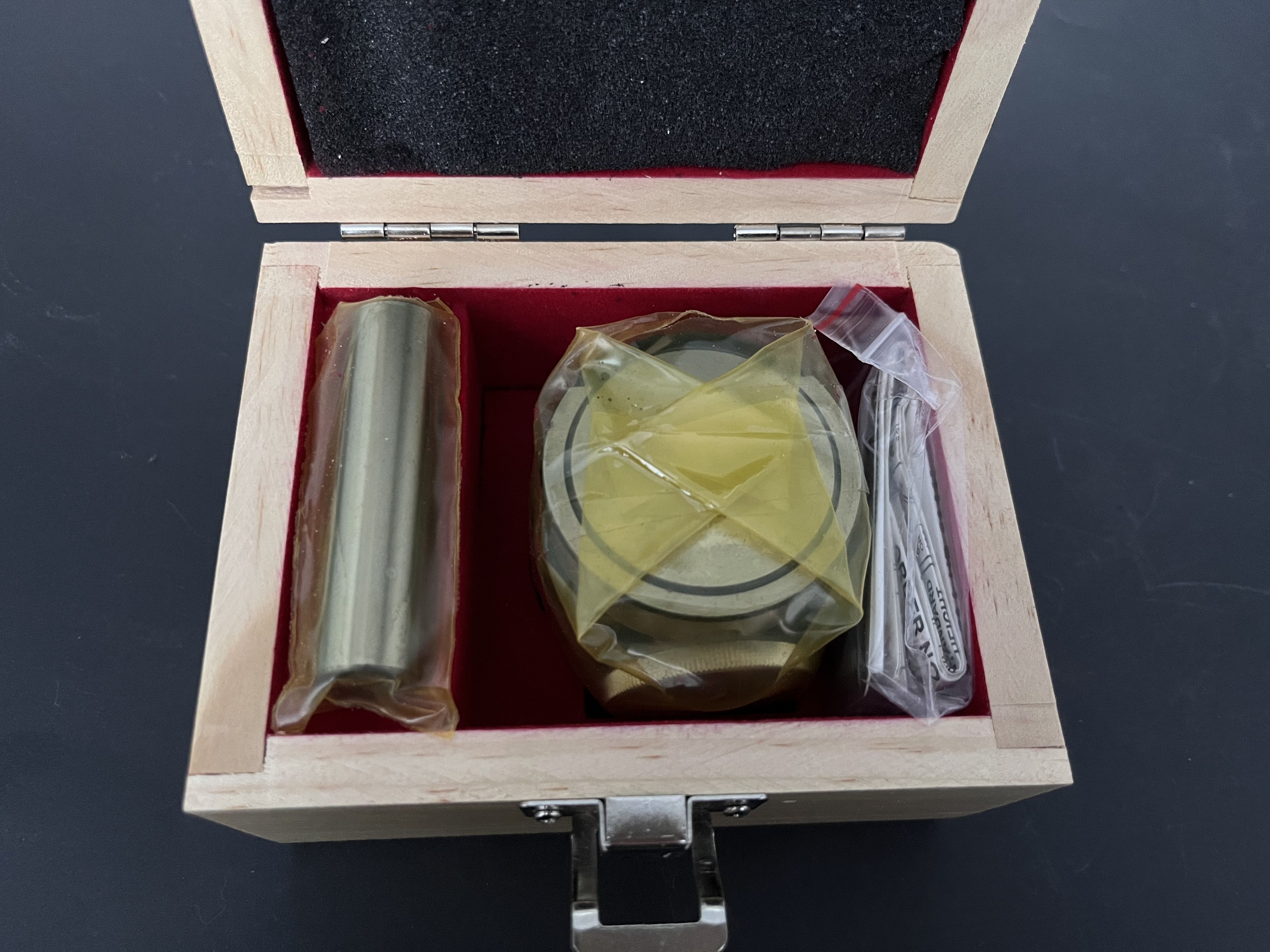

ส่วนที่ 1
ชิ้นงาน overcut:

เหตุผล:
1) เพื่อตีกลับเครื่องตัดเครื่องมือไม่แข็งแรงพอและยาวเกินไปหรือเล็กเกินไปทำให้เครื่องมือตีกลับ
2) การทำงานที่ไม่เหมาะสมโดยผู้ประกอบการ
3) ค่าเผื่อการตัดที่ไม่สม่ำเสมอ (ตัวอย่างเช่น: ทิ้ง 0.5 ที่ด้านข้างของพื้นผิวโค้งและ 0.15 ที่ด้านล่าง) 4) พารามิเตอร์การตัดที่ไม่เหมาะสม (ตัวอย่างเช่น: ความอดทนมีขนาดใหญ่เกินไปการตั้งค่า SF เร็วเกินไป ฯลฯ )
ทำให้ดีขึ้น:
1) ใช้หลักการตัด: มันอาจใหญ่ แต่ไม่เล็กมันอาจสั้น แต่ไม่นาน
2) เพิ่มขั้นตอนการทำความสะอาดมุมและพยายามรักษาระยะขอบให้เท่าที่จะทำได้ (ระยะขอบด้านข้างและด้านล่างควรสอดคล้องกัน)
3) ปรับพารามิเตอร์การตัดอย่างสมเหตุสมผลและรอบมุมด้วยระยะขอบขนาดใหญ่
4) การใช้ฟังก์ชั่น SF ของเครื่องมือเครื่องจักรผู้ปฏิบัติงานสามารถปรับความเร็วได้อย่างละเอียดเพื่อให้ได้เอฟเฟกต์การตัดที่ดีที่สุดของเครื่องมือเครื่องจักร

ตอนที่ 2
ปัญหาการตั้งค่าเครื่องมือ

เหตุผล:
1) ผู้ประกอบการไม่ถูกต้องเมื่อทำงานด้วยตนเอง
2) เครื่องมือถูกยึดอย่างไม่ถูกต้อง
3) ใบมีดบนเครื่องตัดการบินไม่ถูกต้อง (เครื่องตัดการบินเองมีข้อผิดพลาดบางอย่าง)
4) มีข้อผิดพลาดระหว่างคัตเตอร์ R, คัตเตอร์แบนและเครื่องตัดการบิน
ทำให้ดีขึ้น:
1) การดำเนินการด้วยตนเองควรได้รับการตรวจสอบอย่างระมัดระวังซ้ำ ๆ และควรตั้งค่าเครื่องมือที่จุดเดียวกันให้มากที่สุด
2) เมื่อติดตั้งเครื่องมือให้เป่าทำความสะอาดด้วยปืนลมหรือเช็ดทำความสะอาดด้วยผ้าขี้ริ้ว
3) เมื่อต้องวัดใบมีดบนเครื่องตัดการบินบนตัวยึดเครื่องมือและพื้นผิวด้านล่างขัดสามารถใช้ใบมีดได้
4) ขั้นตอนการตั้งค่าเครื่องมือแยกต่างหากสามารถหลีกเลี่ยงข้อผิดพลาดระหว่างเครื่องตัด r, เครื่องตัดแบนและเครื่องตัดการบิน

ส่วนที่ 3
การเขียนโปรแกรม

เหตุผล:
1) ความสูงด้านความปลอดภัยไม่เพียงพอหรือไม่ตั้งค่า (ตัวตัดหรือชัคกระทบชิ้นงานในช่วงฟีด G00 อย่างรวดเร็ว)
2) เครื่องมือในรายการโปรแกรมและเครื่องมือโปรแกรมจริงถูกเขียนอย่างไม่ถูกต้อง
3) ความยาวเครื่องมือ (ความยาวของใบมีด) และความลึกการประมวลผลจริงบนแผ่นงานโปรแกรมถูกเขียนอย่างไม่ถูกต้อง
4) การดึงแกน z เชิงลึกและการดึงแกน z จริงถูกเขียนอย่างไม่ถูกต้องบนแผ่นโปรแกรม
5) พิกัดถูกตั้งค่าไม่ถูกต้องในระหว่างการเขียนโปรแกรม
ทำให้ดีขึ้น:
1) วัดความสูงของชิ้นงานอย่างถูกต้องและตรวจสอบให้แน่ใจว่าความสูงที่ปลอดภัยนั้นสูงกว่าชิ้นงาน
2) เครื่องมือในรายการโปรแกรมจะต้องสอดคล้องกับเครื่องมือโปรแกรมจริง (ลองใช้รายการโปรแกรมอัตโนมัติหรือใช้รูปภาพเพื่อสร้างรายการโปรแกรม)
3) วัดความลึกที่แท้จริงของการประมวลผลบนชิ้นงานและเขียนความยาวและความยาวใบมีดของเครื่องมือบนแผ่นโปรแกรมอย่างชัดเจน (โดยทั่วไปความยาวของตัวหนีบเครื่องมือจะสูงกว่าชิ้นงาน 2-3 มม. และความยาวของใบมีดคือ 0.5-1.0 มม.)
4) ใช้หมายเลข Z-Axis จริงบนชิ้นงานและเขียนลงบนแผ่นงานโปรแกรมอย่างชัดเจน (โดยทั่วไปการดำเนินการนี้เขียนด้วยตนเองและจำเป็นต้องตรวจสอบซ้ำ ๆ )

ตอนที่ 4
ผู้ดำเนินการ

เหตุผล:
1) ข้อผิดพลาดการตั้งค่าเครื่องมือแกน z ความลึก·
2) จำนวนคะแนนถูกตีและการดำเนินการผิด (เช่น: การดึงข้อมูลฝ่ายเดียวโดยไม่มีรัศมีฟีด ฯลฯ )
3) ใช้เครื่องมือที่ไม่ถูกต้อง (ตัวอย่างเช่น: ใช้เครื่องมือ D4 กับเครื่องมือ D10 สำหรับการประมวลผล)
4) โปรแกรมผิดพลาด (ตัวอย่างเช่น: A7.NC ไปที่ A9.NC)
5) Handwheel หมุนไปในทิศทางที่ผิดระหว่างการทำงานด้วยตนเอง
6) กดทิศทางที่ไม่ถูกต้องในระหว่างการสำรวจอย่างรวดเร็วด้วยตนเอง (ตัวอย่างเช่น: -x กด +x)
ทำให้ดีขึ้น:
1) เมื่อทำการตั้งค่าเครื่องมือ Z-Axis ลึกคุณต้องใส่ใจกับตำแหน่งที่กำลังตั้งค่าเครื่องมือ (พื้นผิวด้านล่างพื้นผิวด้านบนพื้นผิวการวิเคราะห์ ฯลฯ )
2) ตรวจสอบจำนวนการเข้าชมและการดำเนินการซ้ำ ๆ หลังจากเสร็จสิ้น
3) เมื่อติดตั้งเครื่องมือให้ตรวจสอบซ้ำ ๆ ด้วยแผ่นโปรแกรมและโปรแกรมก่อนติดตั้ง
4) โปรแกรมจะต้องติดตามทีละรายการตามลำดับ
5) เมื่อใช้การดำเนินการด้วยตนเองผู้ปฏิบัติงานจะต้องปรับปรุงความสามารถของเขาในการใช้งานเครื่องมือเครื่องจักร
6) เมื่อเคลื่อนไหวด้วยตนเองอย่างรวดเร็วคุณสามารถยกแกน Z ไปยังชิ้นงานก่อนที่จะย้าย

ส่วนที่ 5
ความแม่นยำของพื้นผิว

เหตุผล:
1) พารามิเตอร์การตัดนั้นไม่มีเหตุผลและพื้นผิวชิ้นงานมีความหยาบ
2) ขอบตัดของเครื่องมือไม่คมชัด
3) การยึดเครื่องมือนั้นยาวเกินไปและการกวาดล้างใบมีดนั้นยาวเกินไป
4) การกำจัดชิปการเป่าลมและการล้างน้ำมันไม่ดี
5) วิธีการให้อาหารเครื่องมือการเขียนโปรแกรม (คุณสามารถลองพิจารณาการกัดลง)
6) ชิ้นงานมีเสี้ยน
ทำให้ดีขึ้น:
1) พารามิเตอร์การตัดค่าความคลาดเคลื่อนค่าเผื่อความเร็วและการตั้งค่าฟีดจะต้องสมเหตุสมผล
2) เครื่องมือต้องการให้ผู้ประกอบการตรวจสอบและแทนที่เป็นครั้งคราว
3) เมื่อยึดเครื่องมือผู้ปฏิบัติงานจะต้องทำให้แคลมป์สั้นที่สุดเท่าที่จะเป็นไปได้และใบมีดไม่ควรนานเกินไปที่จะหลีกเลี่ยงอากาศ
4) สำหรับการตัดด้วยมีดแบนมีด R และมีดจมูกกลมความเร็วและการตั้งค่าอาหารสัตว์จะต้องสมเหตุสมผล
5) ชิ้นงานมีเสี้ยน: มันเกี่ยวข้องโดยตรงกับเครื่องมือเครื่องเครื่องมือเครื่องมือและวิธีการให้อาหารเครื่องมือของเราดังนั้นเราจึงต้องเข้าใจประสิทธิภาพของเครื่องมือเครื่องจักรและทำขึ้นสำหรับขอบด้วยเสี้ยน

ตอนที่ 6
ขอบบิ่น

1) ฟีดเร็วเกินไป-ช้าลงไปที่ความเร็วในการป้อนที่เหมาะสม
2) ฟีดเร็วเกินไปที่จุดเริ่มต้นของการตัด-ช้าลงความเร็วในการป้อนที่จุดเริ่มต้นของการตัด
3) แคลมป์หลวม (เครื่องมือ) - แคลมป์
4) แคลมป์หลวม (ชิ้นงาน) - แคลมป์
5) ความแข็งแกร่งไม่เพียงพอ (เครื่องมือ) - ใช้เครื่องมือที่สั้นที่สุดที่อนุญาตให้ยึดที่จับลึกขึ้นและลองทำสี
6) ขอบตัดของเครื่องมือมีความคมชัดเกินไป - เปลี่ยนมุมขอบตัดที่เปราะบางขอบหลัก
7) เครื่องมือเครื่องจักรและตัวยึดเครื่องมือนั้นไม่เพียงพอ - ใช้เครื่องมือเครื่องจักรและตัวยึดเครื่องมือที่มีความแข็งแกร่งที่ดี

ส่วนที่ 7
สึกหรอ

1) ความเร็วของเครื่องเร็วเกินไป - ช้าลงและเพิ่มสารหล่อเย็นให้เพียงพอ
2) เครื่องมือตัดวัสดุขั้นสูงและวัสดุเครื่องมือที่ใช้งานให้แข็งและเพิ่มวิธีการบำบัดพื้นผิว
3) การยึดเกาะของชิป - เปลี่ยนความเร็วฟีดขนาดชิปหรือใช้น้ำมันระบายความร้อนหรือปืนลมเพื่อทำความสะอาดชิป
4) ความเร็วฟีดไม่เหมาะสม (ต่ำเกินไป) - เพิ่มความเร็วในการป้อนและลองทำมิลลิ่ง
5) มุมตัดไม่เหมาะสม-เปลี่ยนเป็นมุมตัดที่เหมาะสม
6) มุมบรรเทาเบื้องต้นของเครื่องมือมีขนาดเล็กเกินไป - เปลี่ยนเป็นมุมบรรเทาที่ใหญ่กว่า

ตอนที่ 8
รูปแบบการสั่นสะเทือน

1) ความเร็วในการป้อนและการตัดนั้นเร็วเกินไป-แก้ไขความเร็วของฟีดและการตัด
2) ความแข็งแกร่งไม่เพียงพอ (เครื่องมือเครื่องจักรและตัวยึดเครื่องมือ)-ใช้เครื่องมือเครื่องจักรที่ดีขึ้นและที่ยึดเครื่องมือหรือเปลี่ยนเงื่อนไขการตัด
3) มุมบรรเทาทุกข์มีขนาดใหญ่เกินไป - เปลี่ยนเป็นมุมบรรเทาที่เล็กลงและประมวลผลขอบ (ใช้ whetstone เพื่อลับขอบหนึ่งครั้ง)
4) แคลมป์หลวม-ยึดชิ้นงาน
5) พิจารณาปริมาณความเร็วและฟีด
ความสัมพันธ์ระหว่างสามปัจจัยของความเร็วความลึกฟีดและความลึกการตัดเป็นปัจจัยที่สำคัญที่สุดในการพิจารณาผลการตัด ฟีดและความเร็วที่ไม่เหมาะสมมักจะนำไปสู่การผลิตที่ลดลงคุณภาพงานชิ้นงานที่ไม่ดีและความเสียหายของเครื่องมืออย่างรุนแรง
เวลาโพสต์: ม.ค.-03-2024