Czynniki, od geometrii i wymiarów części obrabianej po materiał obrabiania, należy wziąć pod uwagę przy wyborze prawafrezowanie nożado zadania obróbki.
Myfrowanie twarzy z nóżkiem ramion 90 ° jest dość powszechne w sklepach maszynowych. W niektórych przypadkach ten wybór jest uzasadniony. Jeśli obrabiany element, który ma być zmienny, ma nieregularny kształt lub powierzchnia odlewu spowoduje różnicę głębokości cięcia, najlepszym wyborem może być młyn naramienny. Ale w innych przypadkach bardziej korzystne może być wybór standardowego młyna 45 °.
Gdy kąt zanurzania frezarki jest mniejszy niż 90 °, grubość wiórów osiowych będzie mniejsza niż szybkość zasilacza frezarki z powodu przerzedzania układów, a kąt spadania frutu będzie miał duży wpływ na obowiązującą paszę na ząb. W mieleniu twarzy młyn do twarzy z kątem spadku 45 ° powoduje cieńsze układy. W miarę zmniejszania się kąta spadku grubość wiórów staje się mniejsza niż zasilacz na ząb, co z kolei zwiększa szybkość zasilającej współczynnik 1,4 razy. W takim przypadku, jeśli zastosowano młyn do kątu spadku 90 °, wydajność jest zmniejszona o 40%, ponieważ nie można osiągnąć efektu przerzedzania chipów osiowych 45 °.
Kolejny ważny aspekt wyboru frezarki jest często pomijany przez użytkowników - wielkość noża do mielenia. Wiele sklepów stoi w obliczu mielenia dużych części, takich jak bloki silnika lub struktury samolotów, przy użyciu noży o mniejszej średnicy, co pozostawia dużo miejsca na zwiększoną wydajność. Idealnie, noża mielenia powinna mieć 70% najnowocześniejszego krawędzi zaangażowanych w cięcie. Na przykład podczas mielenia wielu powierzchni dużej części młyn do twarzy o średnicy 50 mm będzie miał tylko 35 mm cięcia, zmniejszając wydajność. Znaczące oszczędności czasu obróbki można osiągnąć, jeśli zastosowana jest noża o większej średnicy.
Innym sposobem na poprawę operacji mielenia jest optymalizacja strategii mielenia młynów twarzy. Podczas frezowania programowania użytkownik musi najpierw zastanowić się, w jaki sposób narzędzie zanurzy się w przedmiot obrabiany. Często frezowanie noża po prostu przecinało bezpośrednio w przedmiot. Tego typu cięcia zwykle towarzyszy dużo szumu uderzenia, ponieważ gdy wkładka wychodzi z cięcia, chip generowany przez frezarkę jest najgrubsza. Wysoki wpływ wkładki na materiał obrabia ma tendencję do powodowania wibracji i powodowania naprężeń rozciągających, które skracają żywotność narzędzia.
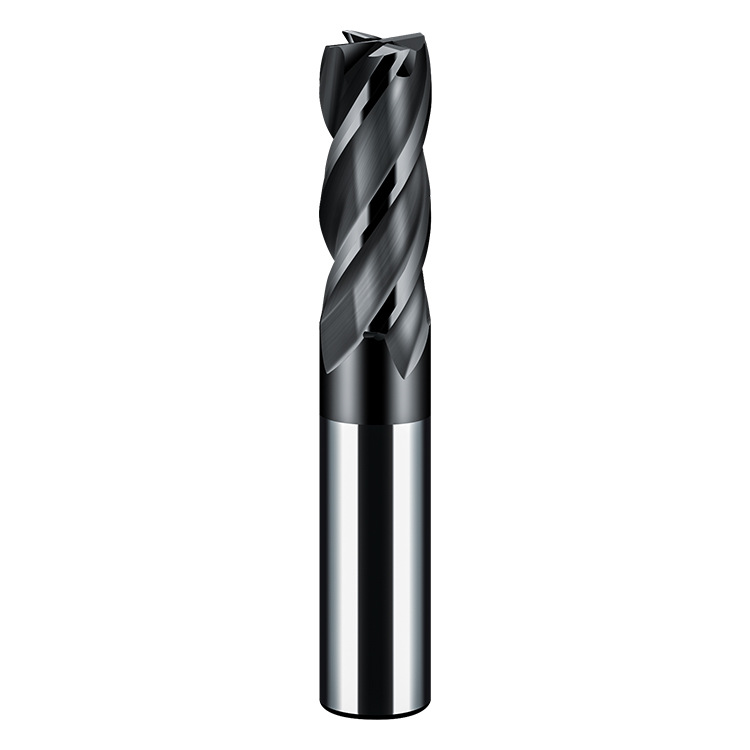
Czas po: 12-2022