Factors ranging from the geometry and dimensions of the part being machined to the material of the workpiece must be considered when selecting the right milling cutter for the machining task.
Face milling with a 90° shoulder cutter is quite common in machine shops. In some cases, this choice is justified. If the workpiece to be milled has an irregular shape, or the surface of the casting will cause the depth of cut to vary, a shoulder mill may be the best choice. But in other cases, it may be more beneficial to opt for a standard 45° face mill.
When the plunging angle of the milling cutter is less than 90°, the axial chip thickness will be smaller than the feed rate of the milling cutter due to the thinning of the chips, and the milling cutter plunging angle will have a great influence on the applicable feed per tooth. In face milling, a face mill with a 45° plunging angle results in thinner chips. As the plunge angle decreases, the chip thickness becomes less than the feed per tooth, which in turn increases the feed rate by a factor of 1.4 times. In this case, if a face mill with a 90° plunging angle is used, productivity is reduced by 40% because the axial chip thinning effect of a 45° face mill cannot be achieved.
Another important aspect of choosing a milling cutter is often overlooked by users - the size of the milling cutter. Many shops face milling of large parts, such as engine blocks or aircraft structures, using smaller diameter cutters, which leaves a lot of room for increased productivity. Ideally, the milling cutter should have 70% of the cutting edge involved in cutting. For example, when milling multiple surfaces of a large part, a face mill with a diameter of 50mm will have only 35mm of the cut, reducing productivity. Significant machining time savings can be achieved if a larger diameter cutter is used.
Another way to improve milling operations is to optimize the milling strategy of face mills. When programming face milling, the user must first consider how the tool will plunge into the workpiece. Often, milling cutters simply cut directly into the workpiece. This type of cut is usually accompanied by a lot of impact noise, because when the insert exits the cut, the chip generated by the milling cutter is the thickest. The high impact of the insert on the workpiece material tends to cause vibration and create tensile stresses that shorten tool life.
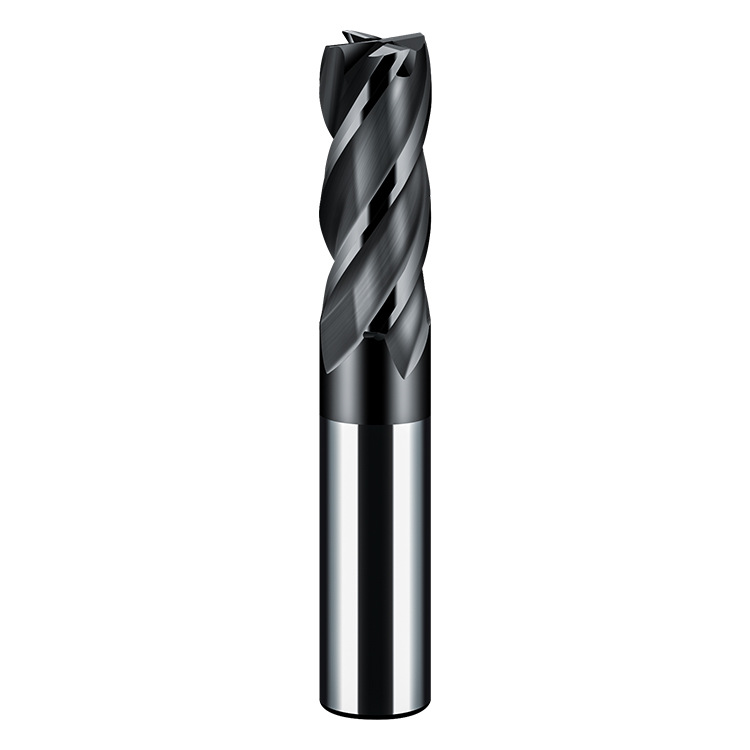
Post time: May-12-2022