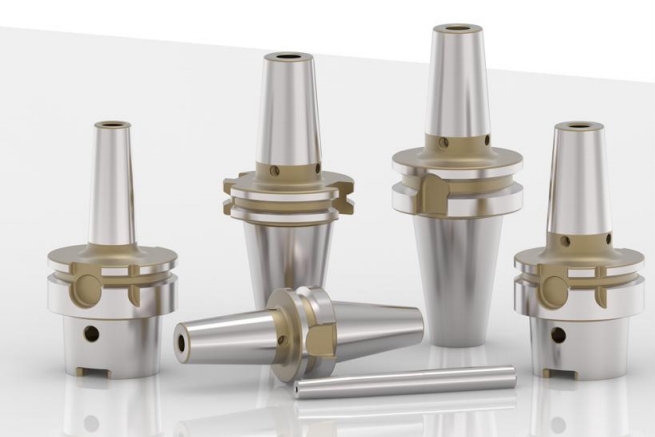

Part 1

In the world of manufacturing and precision engineering, the expansion tool holder has emerged as a groundbreaking solution, revolutionizing the clamping process and setting new standards for performance. At the core of its design lies the principle of thermal expansion and contraction, setting it apart as a game-changer in the industry.
Principle of Expansion Tool Holder Clamping The expansion tool holder operates on the fundamental principle of thermal expansion and contraction, harnessing the power of heat to achieve optimal clamping. Through the utilization of a heat induction device, the clamping portion of the tool undergoes rapid heating, triggering the expansion of the inner diameter of the tool holder. Subsequently, the tool is seamlessly inserted into the expanded tool holder, and upon cooling, the tool holder contracts, exerting a uniform clamping force with the absence of mechanical clamping components.
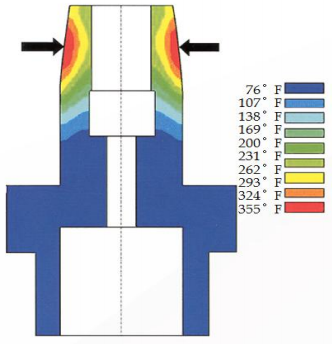

Part 2

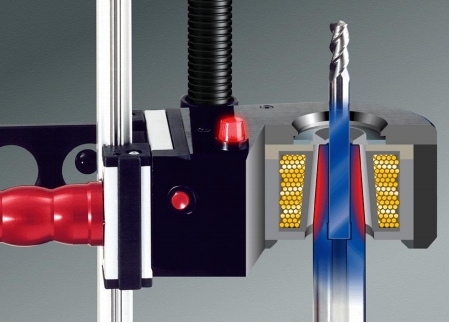
Characteristics of the Expansion Tool Holder This innovative clamping solution boasts an array of impressive characteristics that set it apart from traditional methods:
Minimal tool deflection (≤3μm) and robust clamping force due to uniform clamping
Compact and symmetrical design with small external dimensions, making it ideal for deep cavity machining
Versatile adaptability to high-speed machining, offering significant advantages in both rough and finish machining processes
Enhanced cutting speed, feed rate, and surface finish, ultimately extending the lifespan of both the tool and spindle
Solid carbide tooling clamped with the expansion tool holder can experience a remarkable increase in tool life by over 30%, alongside a 30% efficiency improvement, cementing its status as a high-precision and high-rigidity clamping tool holder.
Usage of the Expansion Tool Holder To maximize the potential of the expansion tool holder, it is recommended to employ it for clamping tooling with cylindrical shanks. Tools with a diameter of less than 6mm should adhere to a shank tolerance of h5, while those with a diameter of 6mm or more should follow a shank tolerance of h6. While the expansion tool holder is compatible with various tool materials such as high-speed steel, solid carbide, and heavy metal, solid carbide is the preferred choice for optimum performance.

Part 3

Methods for Using and Safety Notes for the Expansion Tool Holder As with any advanced tool, understanding the correct usage and abiding by safety protocols is paramount. During the installation or removal of tools, it's crucial to note that the expansion tool holder can generate temperatures exceeding 300 degrees, with a typical heating time ranging from 5 to 10 seconds. For safety, it is imperative to avoid contact with the heated parts of the tool holder during the clamping process and to wear asbestos gloves while handling the tool holder, mitigating any risk of burns.
Sustainability and Durability The expansion tool holder is not only a beacon of innovation and efficiency but also embodies longevity and reliability. With a minimum service life exceeding 3 years, it stands as a testament to its durable construction and sustainable impact on manufacturing operations.
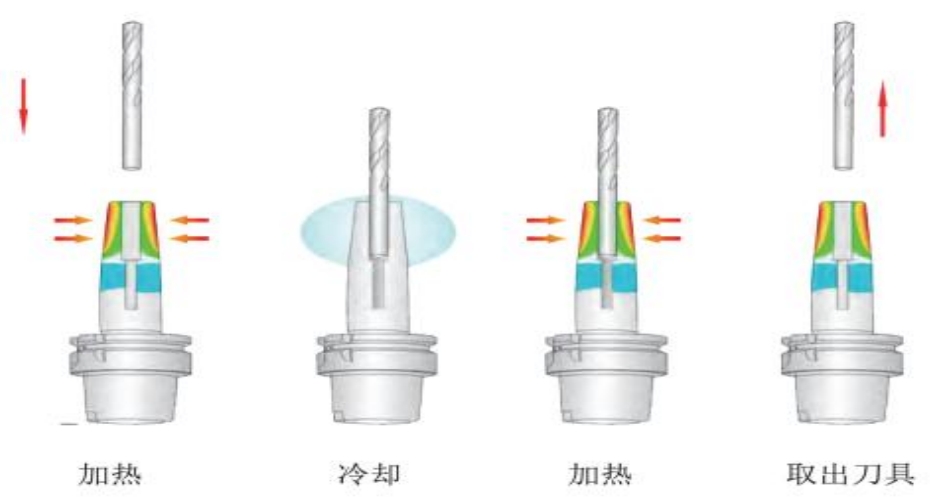
In conclusion, the expansion tool holder represents a leap forward in clamping technology, offering unparalleled precision, efficiency, and reliability. With its transformative impact on the manufacturing landscape, it has cemented its status as an essential tool for modern precision engineering.
Post time: Feb-28-2024