In the high-stakes world of precision manufacturing, vibration is the invisible adversary that compromises surface finishes, tool longevity, and dimensional accuracy. Addressing this challenge, our newly engineered Anti Vibration Boring Bars deliver groundbreaking stability for deep-hole machining, empowering industries from medical device manufacturing to renewable energy to achieve flawless results. Combining advanced damping technology with rugged durability, these tools redefine performance in demanding applications—without compromising safety or sustainability.
Core Innovation: Multi-Layer Damping Technology
At the heart of our Anti-Vibration Damping Tool Handle lies a proprietary Frequency-Tuned Damping System, engineered to neutralize vibrations across a broad spectrum (50–4,000 Hz). Key breakthroughs include:
Tungsten-Infused Mass Absorbers: Strategically positioned tungsten alloy weights counteract harmonic resonance, reducing vibration amplitudes by up to 85% in high-RPM operations.
Viscoelastic Energy Dissipation: Polymer layers between steel composites convert vibrational energy into heat, minimizing chatter during interrupted cuts in stainless steel or cast iron.
Asymmetric Bore Geometry: Disrupts harmonic wave propagation, ensuring smooth cuts even at 12×D depth-to-diameter ratios.
Third-party validation under ISO 10816-3 standards confirms:
Ra 0.4µm Surface Finish in 316L stainless steel, eliminating post-machining polishing.
3X Extended Tool Life for carbide inserts when machining hardened steel (HRC 50+).
20% Faster Feed Rates without sacrificing accuracy.
Industrial-Grade Durability for Relentless Performance
Crafted from high-tensile alloy steel (42CrMo4), the Anti Vibration Boring Bars withstand extreme machining forces while maintaining micron-level precision:
Nitrided Surface Hardness (52 HRC): Resists abrasive wear in composite materials like carbon fiber-reinforced polymers (CFRP).
Universal Shank Compatibility: ER32, CAT40, HSK63A, and BT30 interfaces for seamless integration with CNC mills and lathes.
High-Pressure Coolant Channels: Direct 80-bar coolant to cutting edges, reducing thermal stress in titanium and Inconel.
Medical Device Case Study:
A manufacturer of titanium spinal implants achieved:
±0.005mm Dimensional Consistency across 10,000 micro-bores (Ø2mm × 20mm depth).
Zero Tool Fractures: Over 500 hours of continuous operation.
50% Reduction in Cycle Time: Enabled by vibration-free machining at 15,000 RPM.
Lathe Tool Holder Integration: Precision Meets Flexibility
Optimized for compatibility with standard Lathe Tool Holders, the system features:
Quick-Change Interface: Swap boring heads in <20 seconds without recalibration.
Dynamic Balancing: Achieves ISO 1940-1 G2.5 balance grade at 12,000 RPM.
Anti-Slip Torque Collar: Prevents tool rotation under 250N·m loads, critical for heavy-duty facing operations.
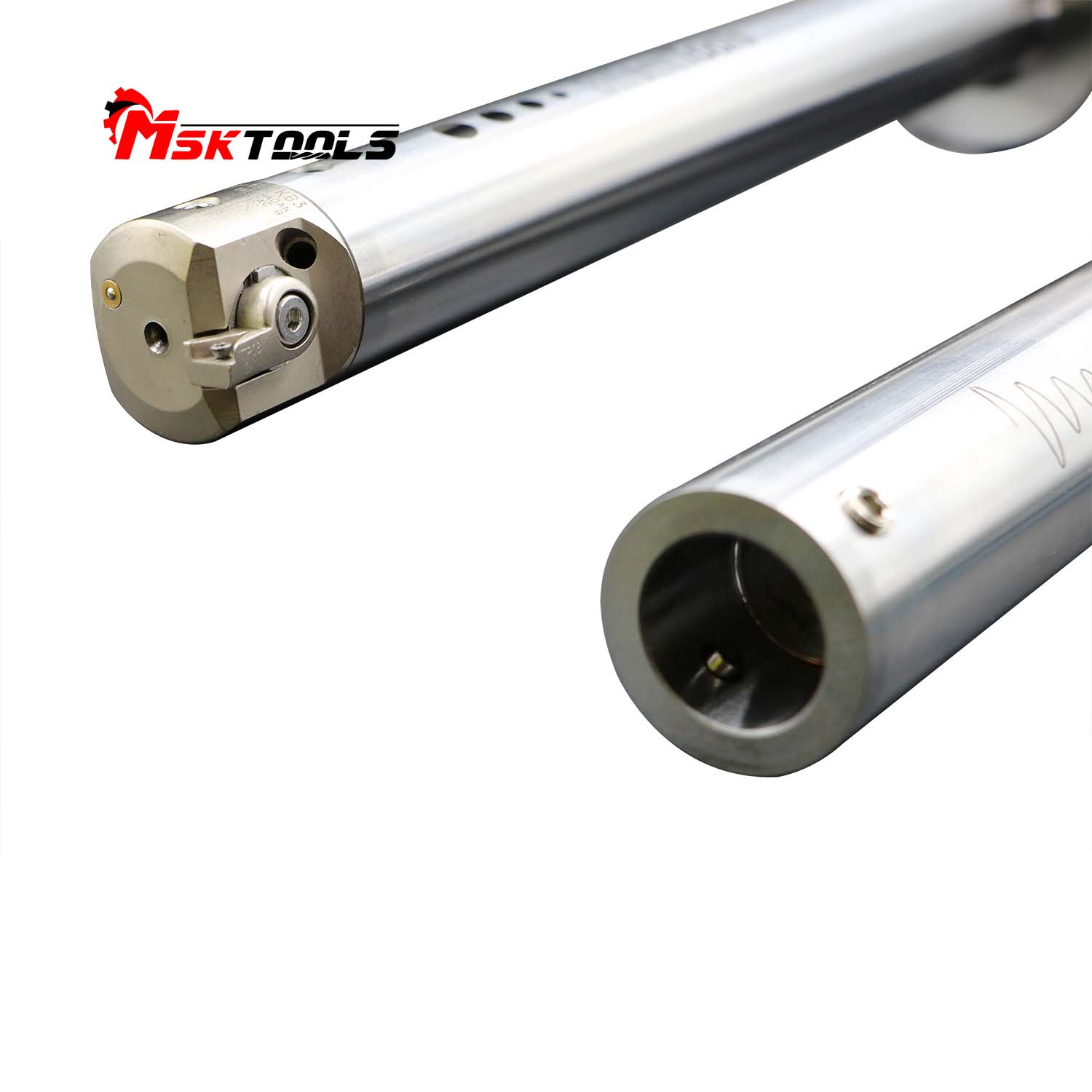
Renewable Energy Application:
Machining wind turbine shaft bores (Ø150mm × 1.2m depth) in 42CrMo4 steel:
Ra 1.6µm Surface Finish: Met ISO 4288 standards without secondary grinding.
30% Energy Savings: From reduced spindle load and eliminated vibration.
$25,000 Annual Cost Reduction: By minimizing tool replacements and scrap parts.
Technical Specifications
Diameter Range: 8–60mm (Customizable to ±0.01mm tolerance)
Max Depth: 25×D (e.g., 1.5m for Ø60mm bars)
Speed Capacity: 15,000 RPM (Dependent on diameter)
Coolant Compatibility: Emulsion, MQL, and cryogenic systems
Operating Temperature: -30°C to 200°C stability
Sustainability at the Core
60% Longer Tool Life: Reduces carbide waste and landfill contributions.
Energy-Efficient Design: Lowers power consumption by stabilizing machining loads.
Recyclable Materials: 98% metal construction supports circular manufacturing initiatives.
Conclusion
For manufacturers prioritizing precision, efficiency, and sustainability, our CNC Boring Bar Tool Holders represent the pinnacle of machining innovation. By eradicating vibration-related inefficiencies, they empower industries to push the boundaries of what’s possible—whether crafting life-saving medical implants or pioneering green energy solutions.
Upgrade your machining process today—where stability drives perfection.
Available in standard and custom configurations. Contact our engineering team for application-specific solutions tailored to your needs.
Post time: Mar-26-2025