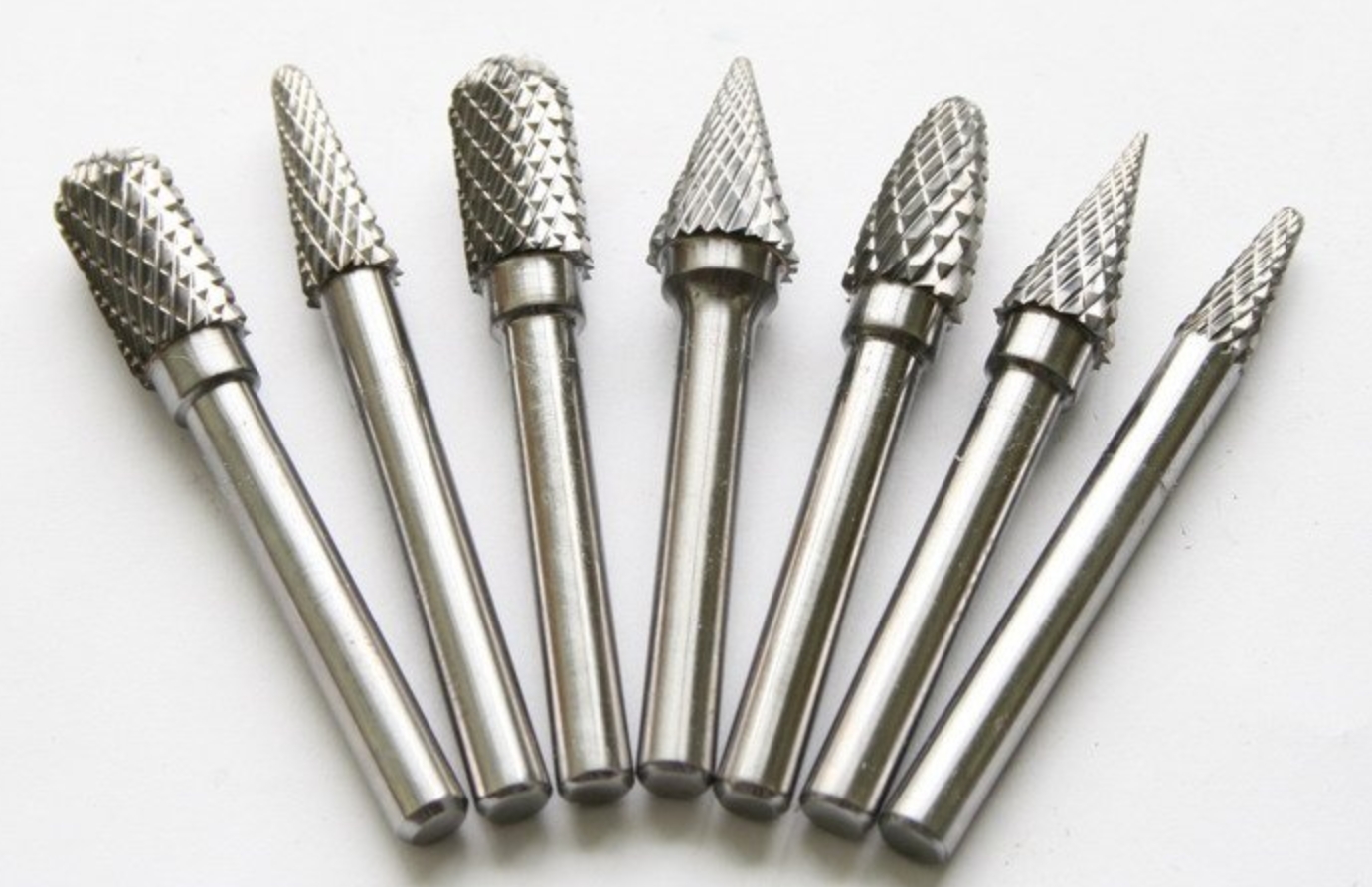
Carbide burrs are essential tools in various industries, including metalworking, woodworking, and engineering. These versatile cutting tools are used for shaping, grinding, and deburring a wide range of materials, making them indispensable for professionals and hobbyists alike. When it comes to high-quality carbide burrs, the MSK brand stands out as a trusted and reliable choice. In this comprehensive guide, we will explore the features, applications, and benefits of carbide burrs, with a specific focus on the MSK brand.

Part 1

Understanding Carbide Burrs
Carbide burrs, also known as rotary files or die grinders, are cutting tools used for shaping, grinding, and removing material from workpieces. They are typically mounted on rotary tools such as die grinders, electric drills, or pneumatic tools, and are available in a variety of shapes, sizes, and cutting configurations to suit different applications.
The cutting edges of carbide burrs are made from tungsten carbide, a hard and durable material that is well-suited for machining tough materials such as steel, stainless steel, cast iron, and non-ferrous metals. This makes carbide burrs ideal for tasks such as deburring, shaping, and grinding, where precision and durability are essential.
MSK Brand: A Trusted Name in Carbide Burrs
MSK is a renowned manufacturer of cutting tools, including carbide burrs, that are known for their exceptional quality, performance, and durability. With a commitment to innovation and precision engineering, MSK has established itself as a leading brand in the industry, offering a wide range of carbide burrs designed to meet the diverse needs of professionals and enthusiasts.

Part 2

Features of MSK Carbide Burrs
MSK carbide burrs are engineered to deliver superior performance and durability, thanks to a range of features that set them apart from other brands. Some of the key features of MSK carbide burrs include:
1. High-Quality Tungsten Carbide: MSK uses premium-grade tungsten carbide to manufacture the cutting edges of their burrs, ensuring exceptional hardness and wear resistance.
2. Precision Machining: Each MSK carbide burr is precision-machined to exacting standards, resulting in sharp and consistent cutting edges that deliver precise and efficient material removal.
3. Versatile Shapes and Configurations: MSK offers a wide variety of burr shapes and cutting configurations to suit different applications, from general-purpose deburring to intricate shaping and grinding tasks.
4. Heat and Wear Resistance: MSK carbide burrs are designed to withstand high temperatures and heavy-duty use, making them suitable for demanding machining applications.

Part 3

Applications of Carbide Burrs
Carbide burrs find applications across a wide range of industries and tasks, thanks to their versatility and precision. Some common applications of carbide burrs include:
1. Deburring: Carbide burrs are used to remove sharp edges and burrs from metal, plastic, and composite materials, resulting in smooth and clean edges.
2. Shaping and Grinding: Carbide burrs are ideal for shaping and grinding tasks, such as creating intricate contours, bevels, and grooves in metal and other materials.
3. Weld Preparation: Carbide burrs are used to prepare weld joints by removing excess material and creating clean, precise edges for welding.
4. Surface Finishing: Carbide burrs can be used for surface finishing tasks, such as blending, smoothing, and polishing metal surfaces.
5. Material Removal: Carbide burrs are effective for rapid material removal in applications such as metal fabrication, woodworking, and mold making.
Benefits of Using MSK Carbide Burrs
Choosing MSK carbide burrs offers a range of benefits that make them a preferred choice for professionals and hobbyists alike. Some of the key benefits of using MSK carbide burrs include:
1. Exceptional Durability: MSK carbide burrs are designed to withstand heavy-duty use and provide long-lasting performance, reducing the need for frequent replacements.
2. Precision and Consistency: MSK burrs are engineered for precision and consistency, ensuring accurate and efficient material removal with minimal effort.
3. Versatility: With a wide range of shapes and cutting configurations, MSK carbide burrs are versatile tools that can handle a variety of tasks across different industries and applications.
4. Heat Resistance: MSK carbide burrs are capable of withstanding high temperatures, making them suitable for demanding machining operations that generate heat.
5. Cost-Effective: Despite their high-quality construction, MSK carbide burrs offer excellent value for money, providing reliable performance at a competitive price point.
Choosing the Right MSK Carbide Burr
When selecting an MSK carbide burr for a specific application, it is important to consider factors such as the material to be machined, the desired cutting profile, and the type of rotary tool being used. MSK offers a comprehensive range of carbide burrs, each designed for specific applications and materials. Some popular MSK carbide burr shapes and configurations include:
1. Cylindrical: Ideal for deburring, shaping, and grinding tasks on flat surfaces and edges.
2. Ball: Suitable for contouring, blending, and shaping concave and convex surfaces.
3. Tree: Designed for rapid material removal and shaping in hard-to-reach areas and contours.
4. Oval: Effective for deburring, shaping, and grinding tasks on curved and irregular surfaces.
5. Flame: Used for rapid material removal and shaping in tight spaces and corners.
It is important to match the burr shape and cutting configuration to the specific requirements of the task at hand, ensuring optimal performance and efficiency.
Tips for Using MSK Carbide Burrs
To maximize the performance and longevity of MSK carbide burrs, it is important to follow some best practices for their use and maintenance. Here are some tips for using MSK carbide burrs effectively:
1. Use the Right Speed: Ensure that the rotary tool is operated at the appropriate speed for the specific burr and material being machined. Excessive speed can cause overheating and premature wear, while insufficient speed may result in inefficient material removal.
2. Apply Proper Pressure: Use light and consistent pressure when using the carbide burr to avoid overheating and premature wear. Let the cutting edges do the work, and avoid forcing the burr into the material.
3. Use Lubrication: When machining hard materials or conducting prolonged cutting operations, using a suitable cutting fluid or lubricant can help reduce heat buildup and prolong the life of the burr.
4. Regular Maintenance: Periodically inspect the carbide burr for signs of wear, damage, or dullness, and replace it if necessary. Keeping the burr clean and free from debris will also help maintain its cutting performance.
5. Safety Precautions: Always wear appropriate personal protective equipment, such as safety glasses and gloves, when using carbide burrs to protect against flying debris and potential hazards.
By following these tips, users can ensure that MSK carbide burrs deliver optimal performance and longevity, making them a valuable investment for their machining needs.
Conclusion
Carbide burrs are indispensable tools for shaping, grinding, and deburring a wide range of materials in various industries. When it comes to high-quality carbide burrs, the MSK brand stands out as a trusted and reliable choice, offering exceptional durability, precision, and versatility. With a comprehensive range of shapes and cutting configurations, MSK carbide burrs are designed to meet the diverse needs of professionals and hobbyists, making them an essential addition to any machining toolkit. By understanding the features, applications, and benefits of MSK carbide burrs, users can make informed decisions and maximize the performance of these essential cutting tools.
Post time: May-17-2024