가공되는 부품의 형상 및 치수에서 공작물의 재료에 이르기까지 오른쪽을 선택할 때는 고려해야합니다.밀링 커터가공 작업을 위해.
어깨 절단기가 90 ° 인 페이스 밀링은 기계 공장에서 매우 일반적입니다. 어떤 경우에는이 선택이 정당화됩니다. Milled가 될 공작물이 불규칙한 모양을 가지거나 주조의 표면으로 인해 절단 깊이가 Ary가 Dary를 유발하는 경우, 어깨 공장이 최선의 선택 일 수 있습니다. 그러나 다른 경우에는 표준 45 ° 페이스 밀을 선택하는 것이 더 유리할 수 있습니다.
밀링 커터의 급락 각도가 90 ° 미만인 경우, 축 방향 칩 두께는 칩의 얇아져 밀링 커터의 공급 속도보다 작을 수 있으며 밀링 커터 급락 각도는 치아 당 적용 가능한 공급에 큰 영향을 미칩니다. 페이스 밀링에서 45 ° 급락 각도가있는 페이스 밀은 칩이 더 얇아집니다. 급락 각도가 감소함에 따라 칩 두께는 치아 당 사료보다 작아지며, 이는 공급 속도를 1.4 배 증가시킵니다. 이 경우, 90 ° 급락 각도가있는 페이스 밀을 사용하는 경우 45 ° 페이스 밀의 축 칩 얇은 효과를 달성 할 수 없기 때문에 생산성이 40% 감소합니다.
밀링 커터를 선택하는 또 다른 중요한 측면은 종종 사용자가 밀링 커터의 크기를 간과합니다. 많은 상점은 직경의 작은 절단기를 사용하여 엔진 블록 또는 항공기 구조와 같은 큰 부품의 밀링을 향하여 생산성을 높일 수있는 많은 공간을 남깁니다. 이상적으로, 밀링 커터는 절단 가장자리의 70%가 절단에 관여해야합니다. 예를 들어, 큰 부분의 여러 표면을 밀링 할 때 직경이 50mm 인 페이스 밀은 컷의 35mm에 불과하여 생산성이 줄어 듭니다. 더 큰 직경 절단기를 사용하는 경우 상당한 가공 시간 절약을 달성 할 수 있습니다.
밀링 작업을 개선하는 또 다른 방법은 얼굴 공장의 밀링 전략을 최적화하는 것입니다. 페이스 밀링을 프로그래밍 할 때는 먼저 도구가 공작물에 빠지는 방법을 고려해야합니다. 종종 밀링 커터는 단순히 공작물로 직접 자릅니다. 이 유형의 컷은 일반적으로 많은 충격 노이즈가 수반됩니다. 삽입이 컷을 종료 할 때 밀링 커터에 의해 생성 된 칩이 가장 두껍기 때문입니다. 공작물 재료에 대한 삽입의 높은 영향은 진동을 일으키고 공구 수명을 단축시키는 인장 응력을 만듭니다.
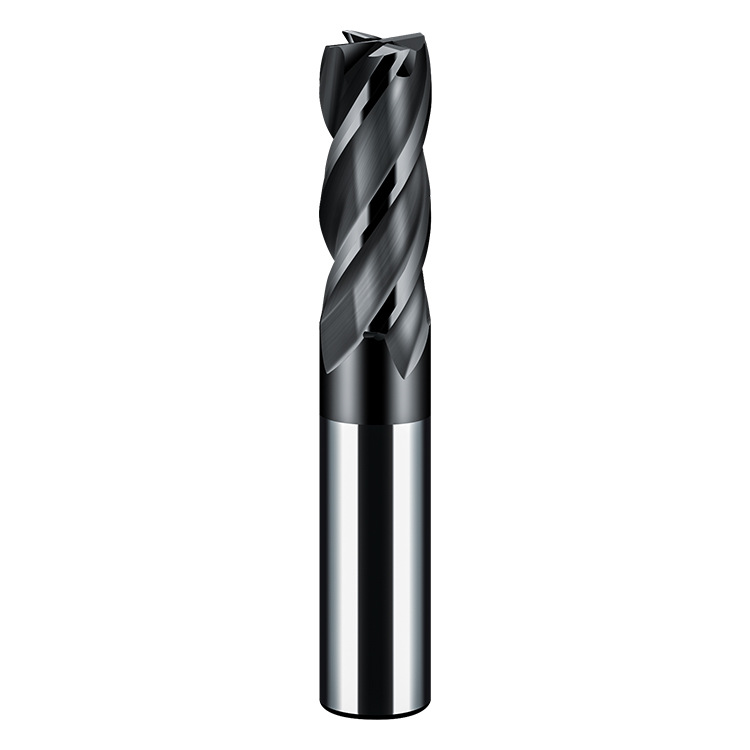
시간 후 : 5 월 12 일