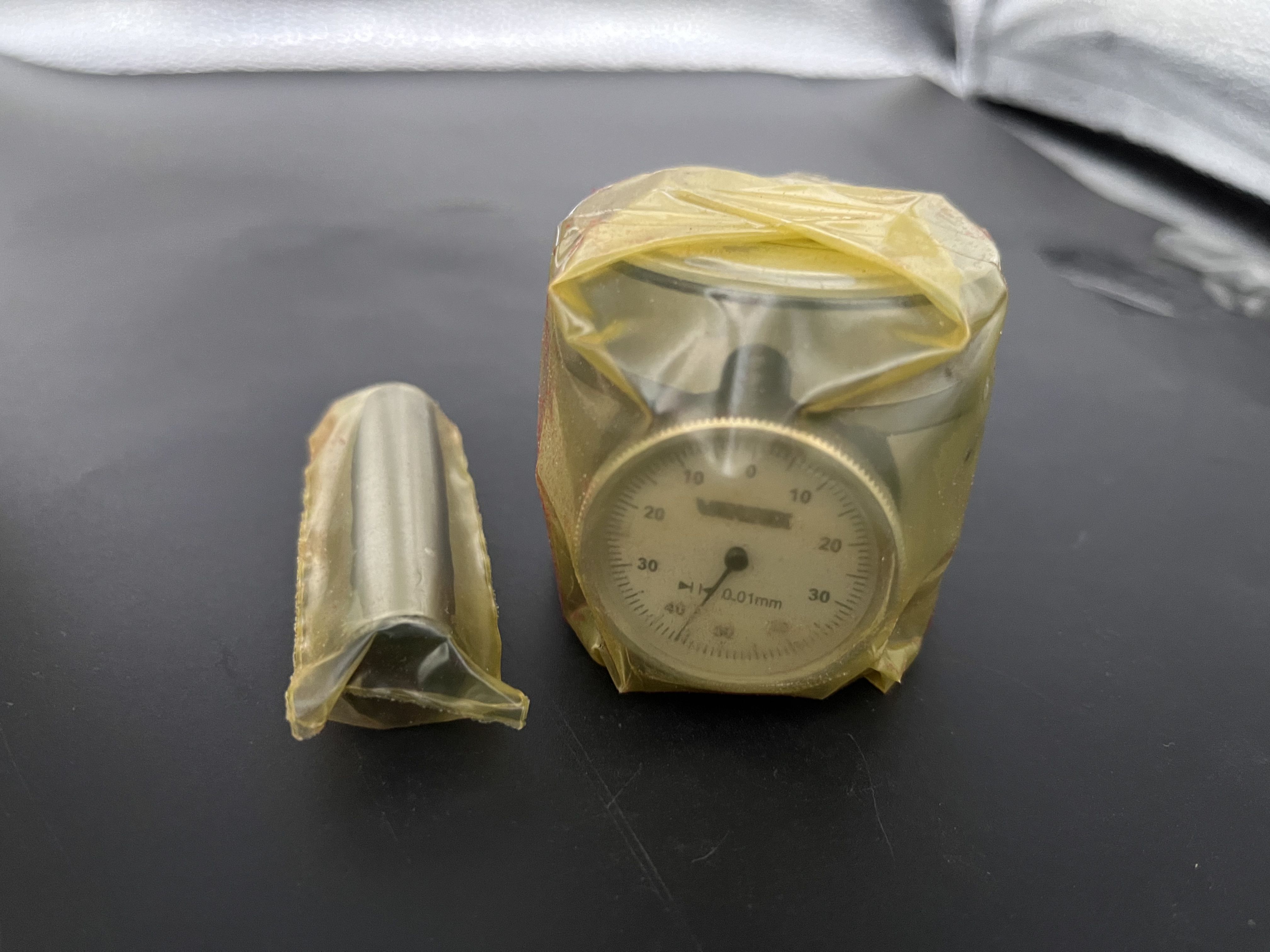
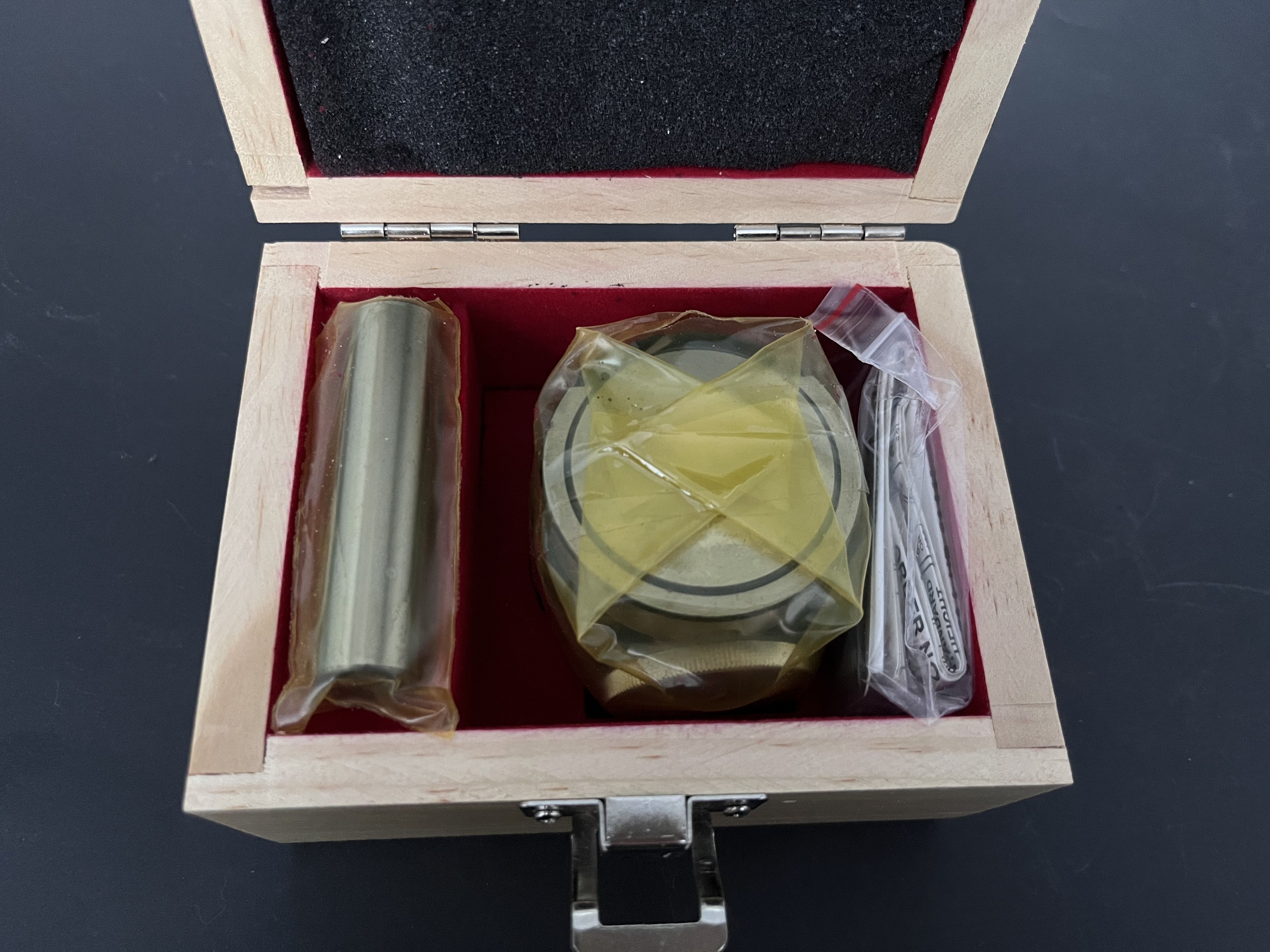

パート1
ワークピースのオーバーカット:

理由:
1) カッターが跳ね返るには、ツールの強度が足りず、ツールが長すぎるか小さすぎるためにツールが跳ね返ることがあります。
2) オペレーターによる不適切な操作。
3) 切削代が不均一 (例: 曲面の側面に 0.5、底面に 0.15 を残す) 4) 切削パラメータが不適切 (例: 許容値が大きすぎる、SF 設定が速すぎるなど)
改善する:
1) カッター原則を使用します。大きくても小さくはならず、短くても長くはなりません。
2) コーナークリーニング手順を追加し、マージンを可能な限り均一に保つようにします(側面と下部のマージンが一貫している必要があります)。
3) 切断パラメータを適切に調整し、余裕を持って角を丸めます。
4) 工作機械の SF 機能を使用すると、オペレーターは速度を微調整して、工作機械の最高の切削効果を実現できます。

パート2
ツール設定の問題

理由:
1) オペレーターが手動で操作する場合、正確ではありません。
2) ツールが正しくクランプされていません。
3) フライングカッターの刃が正しくありません(フライングカッター自体に何らかのエラーがあります)。
4)Rカッター、フラットカッター、フライングカッターの間には誤差があります。
改善する:
1) 手作業は繰り返し注意深く確認し、ツールはできる限り同じポイントにセットするようにしてください。
2) ツールを取り付けるときは、エアガンで吹き飛ばすか、布で拭いてきれいにしてください。
3) フライングカッターの刃をツールホルダー上で測定する必要があり、底面が研磨されている場合は、刃を使用できます。
4) 別々のツール設定手順により、R カッター、フラット カッター、フライング カッター間のエラーを回避できます。

パート3
コライダープログラミング

理由:
1)安全高さが十分でない、または設定されていない(早送りG00中にカッターまたはチャックがワークに当たる)。
2) プログラムリスト上のツールと実際のプログラムツールの記載が間違っています。
3) プログラムシート上の工具長さ(刃長)と実際の加工深さが誤って記載されています。
4) プログラムシートに深さ Z 軸フェッチと実際の Z 軸フェッチが誤って記載されています。
5) プログラミング中に座標が正しく設定されていません。
改善する:
1) ワークピースの高さを正確に測定し、安全な高さがワークピースより上にあることを確認します。
2) プログラム リスト上のツールは、実際のプログラム ツールと一致している必要があります (自動プログラム リストを使用するか、画像を使用してプログラム リストを生成するようにしてください)。
3) ワークの実際の加工深さを測定し、ツールの長さと刃長をプログラムシートに明記します(通常、ツールクランプの長さはワークより2〜3MM高く、刃長は0.5〜1.0MMです)。
4) ワークピース上の実際のZ軸番号を取得し、プログラムシートに明確に記入します。(この操作は通常、手作業で記入し、繰り返し確認する必要があります)。

パート4
衝突型加速器オペレーター

理由:
1)深さZ軸ツール設定エラー。
2) ポイント数がヒットし、操作が間違っている(例:送り半径なしでの片側フェッチなど)。
3) 間違ったツールを使用する (例: 処理に D4 ツールと D10 ツールを使用する)。
4) プログラムにエラーが発生しました (例: A7.NC が A9.NC になりました)。
5) 手動操作中にハンドホイールが間違った方向に回転します。
6) 手動早送り中に間違った方向を押します (例: -X を押す場合は +X を押します)。
改善する:
1) ディープZ軸工具セッティングを行う場合、工具がセットされる場所に注意する必要があります。(底面、上面、解析面など)。
2) 完了後にヒット数や操作数を繰り返し確認します。
3) ツールをインストールする際は、プログラムシートとプログラムで繰り返し確認してからインストールしてください。
4) プログラムは順番に 1 つずつ実行する必要があります。
5) 手動操作を使用する場合、オペレーター自身が工作機械の操作の熟練度を向上させる必要があります。
6) 手動で素早く移動させる場合は、まずZ軸をワークピースまで上げてから移動させることができます。

パート5
表面精度

理由:
1) 切削パラメータが不適切であり、ワークピースの表面が粗い。
2) 工具の刃先が鋭くない。
3) ツールのクランプが長すぎ、ブレードのクリアランスが長すぎます。
4) 切削片の除去、エアブロー、オイルフラッシングは良くありません。
5) ツール送り方法をプログラミングします(ダウンミリングを検討することもできます)。
6) ワークにバリがある。
改善する:
1) 切削パラメータ、許容差、余裕、速度、送り設定は適切でなければなりません。
2) ツールはオペレーターが定期的に点検し、交換する必要があります。
3) ツールをクランプする際、オペレーターはクランプをできるだけ短く保つ必要があり、空気を避けるためにブレードが長すぎないようにする必要があります。
4) フラットナイフ、R ナイフ、丸刃ナイフを使用したダウンカットでは、速度と送りの設定が適切でなければなりません。
5) ワークにバリがある:これは工作機械、工具、工具の送り方法に直接関係しているので、工作機械の性能を理解し、バリのあるエッジを補う必要があります。

パート6
欠けたエッジ

1) 送りが速すぎる - 適切な送り速度まで遅くします。
2) 切削開始時の送り速度が速すぎる - 切削開始時の送り速度を遅くします。
3) クランプを緩める(工具) - クランプ。
4) クランプを緩める(ワークピース) - クランプ。
5) 剛性不足 (ツール) - 許容される最短のツールを使用し、ハンドルをより深く締め付けて、フライス加工を試みます。
6) ツールの刃先が鋭すぎる - 壊れやすい刃先角度、主刃を変更します。
7) 工作機械とツールホルダーの剛性が十分ではありません - 剛性の高い工作機械とツールホルダーを使用してください。

パート7
摩耗

1) 機械の速度が速すぎます - 速度を落とし、十分な量の冷却剤を補充してください。
2) 硬化材料 - 先進的な切削工具と工具材料を使用し、表面処理方法を増やす。
3) チップの付着 - 送り速度やチップのサイズを変更するか、冷却オイルやエアガンを使用してチップを除去します。
4) 送り速度が不適切 (低すぎる) - 送り速度を上げてダウンミリングを試してください。
5) 切断角度が不適切です。適切な切断角度に変更してください。
6) ツールの主逃げ角が小さすぎます。逃げ角を大きく変更してください。

パート8
振動パターン

1) 送り速度と切削速度が速すぎる - 送り速度と切削速度を修正する
2) 剛性不足(工作機械と工具ホルダー) - より良い工作機械と工具ホルダーを使用するか、切削条件を変更する
3) 逃げ角が大きすぎる - 逃げ角を小さくして刃先を加工する(砥石で一度刃先を研ぐ)
4) クランプを緩める - ワークピースをクランプする
5) 速度と送り量を考慮する
切削効果を決定する上で、速度、送り、切込み深さの3つの要素の関係は最も重要な要素です。送りと速度が適切でないと、生産性の低下、ワーク品質の低下、そして深刻な工具損傷につながることがよくあります。
投稿日時: 2024年1月3日