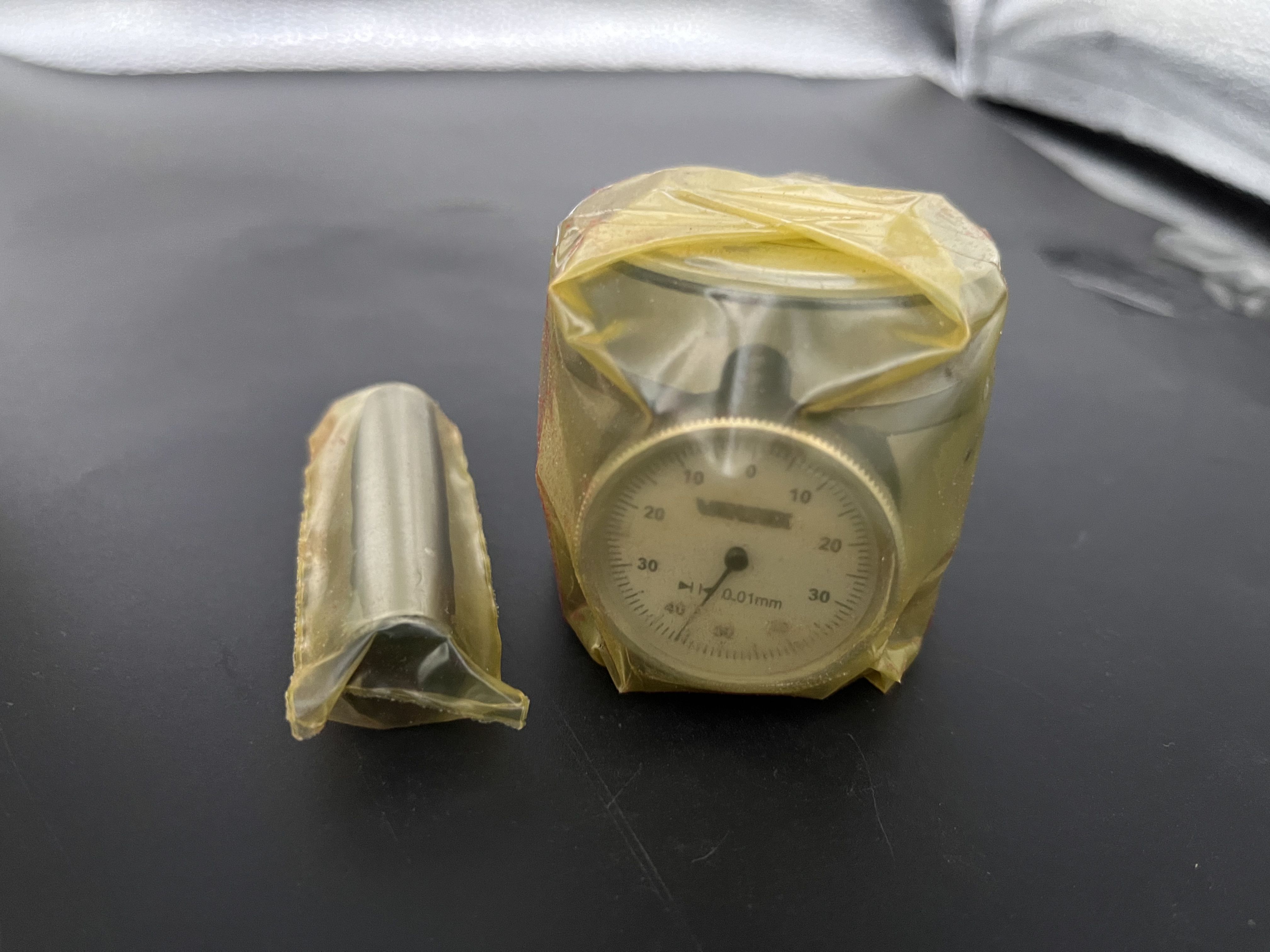
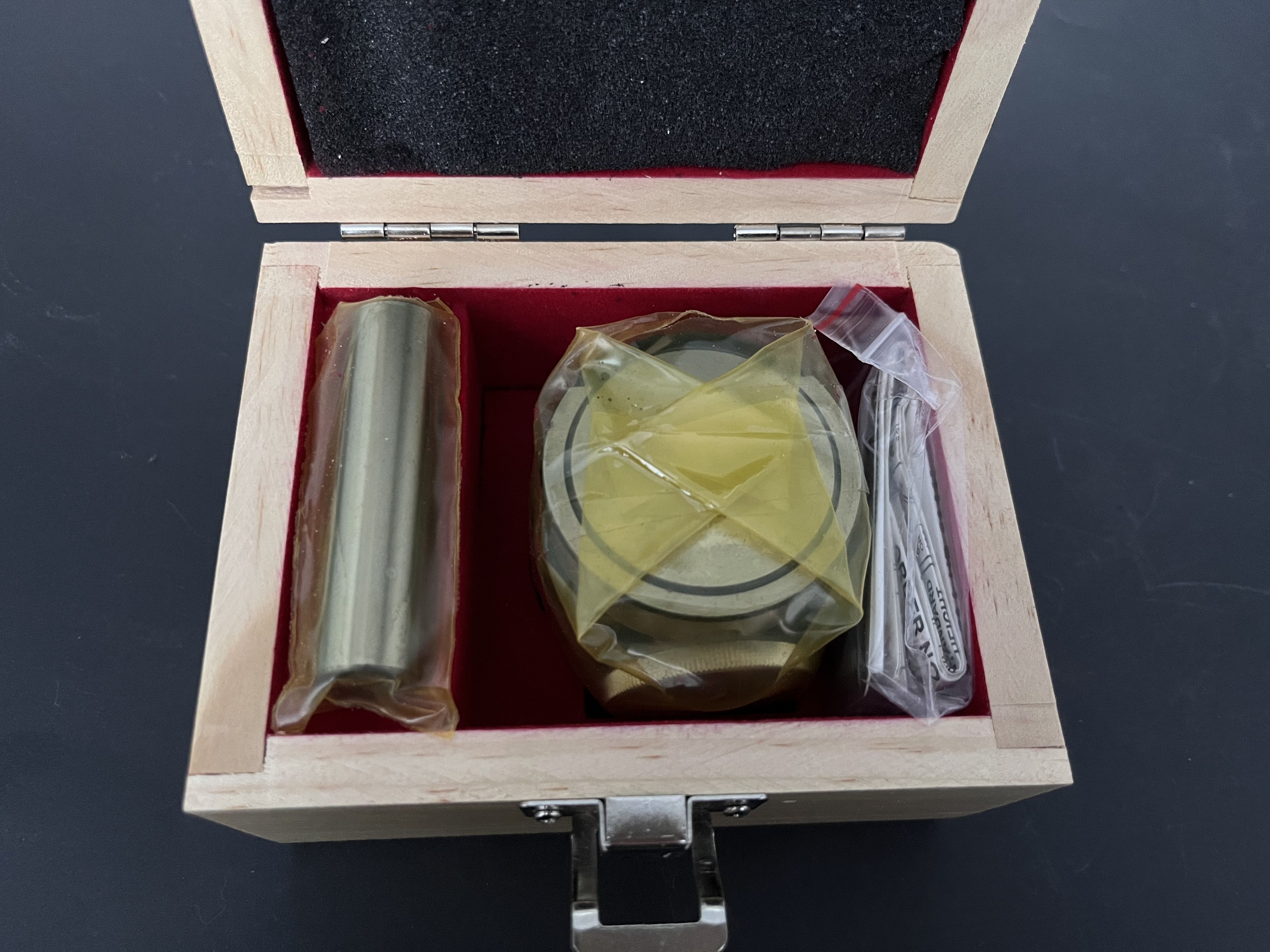

भाग ---- पहला
वर्कपीस ओवरकट:

कारण:
1) कटर को उछालने के लिए उपकरण पर्याप्त मजबूत नहीं है और बहुत लंबा या बहुत छोटा है, जिससे उपकरण उछल जाता है।
2) ऑपरेटर द्वारा अनुचित संचालन।
3) असमान कटिंग भत्ता (उदाहरण के लिए: घुमावदार सतह के किनारे पर 0.5 और नीचे 0.15 छोड़ें) 4) अनुचित कटिंग पैरामीटर (उदाहरण के लिए: सहनशीलता बहुत बड़ी है, एसएफ सेटिंग बहुत तेज है, आदि)
सुधार:
1) कटर सिद्धांत का उपयोग करें: यह बड़ा हो सकता है लेकिन छोटा नहीं, यह छोटा हो सकता है लेकिन लंबा नहीं।
2) कोने की सफाई प्रक्रिया को शामिल करें, और मार्जिन को यथासंभव एक समान रखने का प्रयास करें (किनारे और नीचे का मार्जिन एक समान होना चाहिए)।
3) काटने के मापदंडों को उचित रूप से समायोजित करें और कोनों को बड़े मार्जिन के साथ गोल करें।
4) मशीन टूल के एसएफ फ़ंक्शन का उपयोग करके, ऑपरेटर मशीन टूल के सर्वोत्तम कटिंग प्रभाव को प्राप्त करने के लिए गति को ठीक कर सकता है।

भाग 2
उपकरण सेटिंग समस्या

कारण:
1) ऑपरेटर मैन्युअल रूप से संचालन करते समय सटीक नहीं है।
2) उपकरण गलत तरीके से क्लैंप किया गया है।
3) फ्लाइंग कटर का ब्लेड गलत है (फ्लाइंग कटर में स्वयं कुछ त्रुटियाँ हैं)।
4) आर कटर, फ्लैट कटर और फ्लाइंग कटर के बीच त्रुटि है।
सुधार:
1) मैनुअल संचालन को बार-बार सावधानीपूर्वक जांचना चाहिए, और उपकरण को यथासंभव एक ही बिंदु पर सेट किया जाना चाहिए।
2) उपकरण स्थापित करते समय, इसे एयर गन से साफ करें या कपड़े से पोंछ लें।
3) जब फ्लाइंग कटर पर लगे ब्लेड को टूल होल्डर पर मापने की आवश्यकता हो और निचली सतह को पॉलिश किया गया हो, तो ब्लेड का उपयोग किया जा सकता है।
4) एक अलग टूल सेटिंग प्रक्रिया से आर कटर, फ्लैट कटर और फ्लाइंग कटर के बीच त्रुटियों से बचा जा सकता है।

भाग 3
कोलाइडर-प्रोग्रामिंग

कारण:
1) सुरक्षा ऊंचाई पर्याप्त नहीं है या सेट नहीं है (कटर या चक तीव्र फीड G00 के दौरान वर्कपीस से टकराता है)।
2) प्रोग्राम सूची में दिया गया टूल और वास्तविक प्रोग्राम टूल गलत लिखे गए हैं।
3) प्रोग्राम शीट पर उपकरण की लंबाई (ब्लेड की लंबाई) और वास्तविक प्रसंस्करण गहराई गलत लिखी गई है।
4) गहराई Z-अक्ष फ़ेच और वास्तविक Z-अक्ष फ़ेच प्रोग्राम शीट पर गलत तरीके से लिखे गए हैं।
5) प्रोग्रामिंग के दौरान निर्देशांक गलत तरीके से सेट किए गए हैं।
सुधार:
1) वर्कपीस की ऊंचाई को सटीक रूप से मापें और सुनिश्चित करें कि सुरक्षित ऊंचाई वर्कपीस से ऊपर है।
2) प्रोग्राम सूची के उपकरण वास्तविक प्रोग्राम उपकरणों के अनुरूप होने चाहिए (प्रोग्राम सूची बनाने के लिए स्वचालित प्रोग्राम सूची का उपयोग करें या चित्रों का उपयोग करें)।
3) वर्कपीस पर प्रसंस्करण की वास्तविक गहराई को मापें, और प्रोग्राम शीट पर टूल की लंबाई और ब्लेड की लंबाई स्पष्ट रूप से लिखें (आमतौर पर टूल क्लैंप की लंबाई वर्कपीस से 2-3MM अधिक होती है, और ब्लेड की लंबाई 0.5-1.0MM होती है)।
4) वर्कपीस पर वास्तविक Z-अक्ष संख्या लें और उसे प्रोग्राम शीट पर स्पष्ट रूप से लिखें। (यह प्रक्रिया आमतौर पर मैन्युअल रूप से लिखी जाती है और इसे बार-बार जाँचने की आवश्यकता होती है)।

भाग 4
कोलाइडर-ऑपरेटर

कारण:
1) गहराई Z अक्ष उपकरण सेटिंग त्रुटि·.
2) अंकों की संख्या हिट है और ऑपरेशन गलत है (जैसे: फ़ीड त्रिज्या के बिना एकतरफा फ़ेचिंग, आदि)।
3) गलत उपकरण का उपयोग करें (उदाहरण के लिए: प्रसंस्करण के लिए D10 उपकरण के साथ D4 उपकरण का उपयोग करें)।
4) प्रोग्राम गलत हो गया (उदाहरण के लिए: A7.NC A9.NC में चला गया)।
5) मैनुअल संचालन के दौरान हैंडव्हील गलत दिशा में घूमता है।
6) मैनुअल रैपिड ट्रैवर्स के दौरान गलत दिशा दबाएं (उदाहरण के लिए: -X +X दबाएं)।
सुधार:
1) डीप Z-एक्सिस टूल सेटिंग करते समय, आपको ध्यान देना चाहिए कि टूल कहाँ सेट किया जा रहा है। (नीचे की सतह, ऊपरी सतह, विश्लेषण सतह, आदि)।
2) पूरा होने के बाद बार-बार हिट और ऑपरेशन की संख्या की जांच करें।
3) उपकरण स्थापित करते समय, इसे स्थापित करने से पहले प्रोग्राम शीट और प्रोग्राम से बार-बार जांचें।
4) कार्यक्रम का क्रम से एक-एक करके पालन किया जाना चाहिए।
5) मैनुअल ऑपरेशन का उपयोग करते समय, ऑपरेटर को स्वयं मशीन टूल के संचालन में अपनी दक्षता में सुधार करना चाहिए।
6) मैन्युअल रूप से तेजी से आगे बढ़ते समय, आप आगे बढ़ने से पहले Z-अक्ष को वर्कपीस तक बढ़ा सकते हैं।

भाग 5
सतह की सटीकता

कारण:
1) काटने के पैरामीटर अनुचित हैं और वर्कपीस की सतह खुरदरी है।
2) उपकरण की काटने वाली धार तेज नहीं है।
3) टूल क्लैम्पिंग बहुत लंबी है और ब्लेड क्लीयरेंस भी बहुत लंबा है।
4) चिप हटाना, हवा बहाना और तेल फ्लशिंग अच्छा नहीं है।
5) प्रोग्रामिंग टूल फीडिंग विधि (आप डाउन मिलिंग पर विचार करने का प्रयास कर सकते हैं)।
6) वर्कपीस में गड़गड़ाहट है।
सुधार:
1) काटने के पैरामीटर, सहनशीलता, भत्ते, गति और फ़ीड सेटिंग्स उचित होनी चाहिए।
2) ऑपरेटर को उपकरण की समय-समय पर जांच करने और उसे बदलने की आवश्यकता होती है।
3) उपकरण को क्लैंप करते समय, ऑपरेटर को क्लैंप को यथासंभव छोटा रखना आवश्यक है, और हवा से बचने के लिए ब्लेड बहुत लंबा नहीं होना चाहिए।
4) फ्लैट चाकू, आर चाकू और गोल नाक चाकू के साथ डाउनकटिंग के लिए, गति और फ़ीड सेटिंग्स उचित होनी चाहिए।
5) वर्कपीस में गड़गड़ाहट है: यह सीधे हमारे मशीन टूल, टूल और टूल फीडिंग विधि से संबंधित है, इसलिए हमें मशीन टूल के प्रदर्शन को समझने और गड़गड़ाहट वाले किनारों के लिए बनाने की आवश्यकता है।

भाग 6
छिलता हुआ किनारा

1) बहुत तेज गति से भोजन खिलाएं - उपयुक्त गति तक धीमी गति से खिलाएं।
2) काटने की शुरुआत में फ़ीड बहुत तेज़ है - काटने की शुरुआत में फ़ीड की गति धीमी करें।
3) क्लैंप ढीला (उपकरण) - क्लैंप.
4) क्लैंप ढीला (वर्कपीस) - क्लैंप।
5) अपर्याप्त कठोरता (उपकरण) - अनुमत सबसे छोटे उपकरण का उपयोग करें, हैंडल को अधिक गहराई तक दबाएं, और मिलिंग का प्रयास करें।
6) उपकरण की काटने वाली धार बहुत तेज है - नाजुक काटने वाली धार के कोण, प्राथमिक किनारे को बदलें।
7) मशीन टूल और टूल होल्डर पर्याप्त कठोर नहीं हैं - अच्छी कठोरता वाले मशीन टूल और टूल होल्डर का उपयोग करें।

भाग 7
टूट - फूट

1) मशीन की गति बहुत तेज है - गति धीमी करें और पर्याप्त शीतलक डालें।
2) कठोर सामग्री - उन्नत काटने के उपकरण और उपकरण सामग्री का उपयोग करें, और सतह उपचार विधियों में वृद्धि करें।
3) चिप आसंजन - चिप्स को साफ करने के लिए फीड गति, चिप का आकार बदलें या कूलिंग ऑयल या एयर गन का उपयोग करें।
4) फीड गति अनुपयुक्त है (बहुत कम) - फीड गति बढ़ाएँ और डाउन मिलिंग का प्रयास करें।
5) काटने का कोण अनुपयुक्त है - इसे उचित काटने के कोण में बदलें।
6) उपकरण का प्राथमिक राहत कोण बहुत छोटा है - इसे बड़े राहत कोण में बदलें।

भाग 8
कंपन पैटर्न

1) फीड और कटिंग की गति बहुत तेज़ है - फीड और कटिंग की गति को ठीक करें
2) अपर्याप्त कठोरता (मशीन टूल और टूल होल्डर) - बेहतर मशीन टूल्स और टूल होल्डर का उपयोग करें या काटने की स्थिति बदलें
3) राहत कोण बहुत बड़ा है - इसे एक छोटे राहत कोण में बदलें और किनारे को संसाधित करें (किनारे को एक बार तेज करने के लिए एक छेनी का उपयोग करें)
4) क्लैंप ढीला करें - वर्कपीस को क्लैंप करें
5) गति और फ़ीड मात्रा पर विचार करें
गति, फ़ीड और काटने की गहराई के तीन कारकों के बीच का संबंध काटने के प्रभाव को निर्धारित करने में सबसे महत्वपूर्ण कारक है। अनुचित फ़ीड और गति अक्सर उत्पादन में कमी, वर्कपीस की खराब गुणवत्ता और उपकरण को गंभीर नुकसान पहुँचाती है।
पोस्ट करने का समय: 03 जनवरी 2024