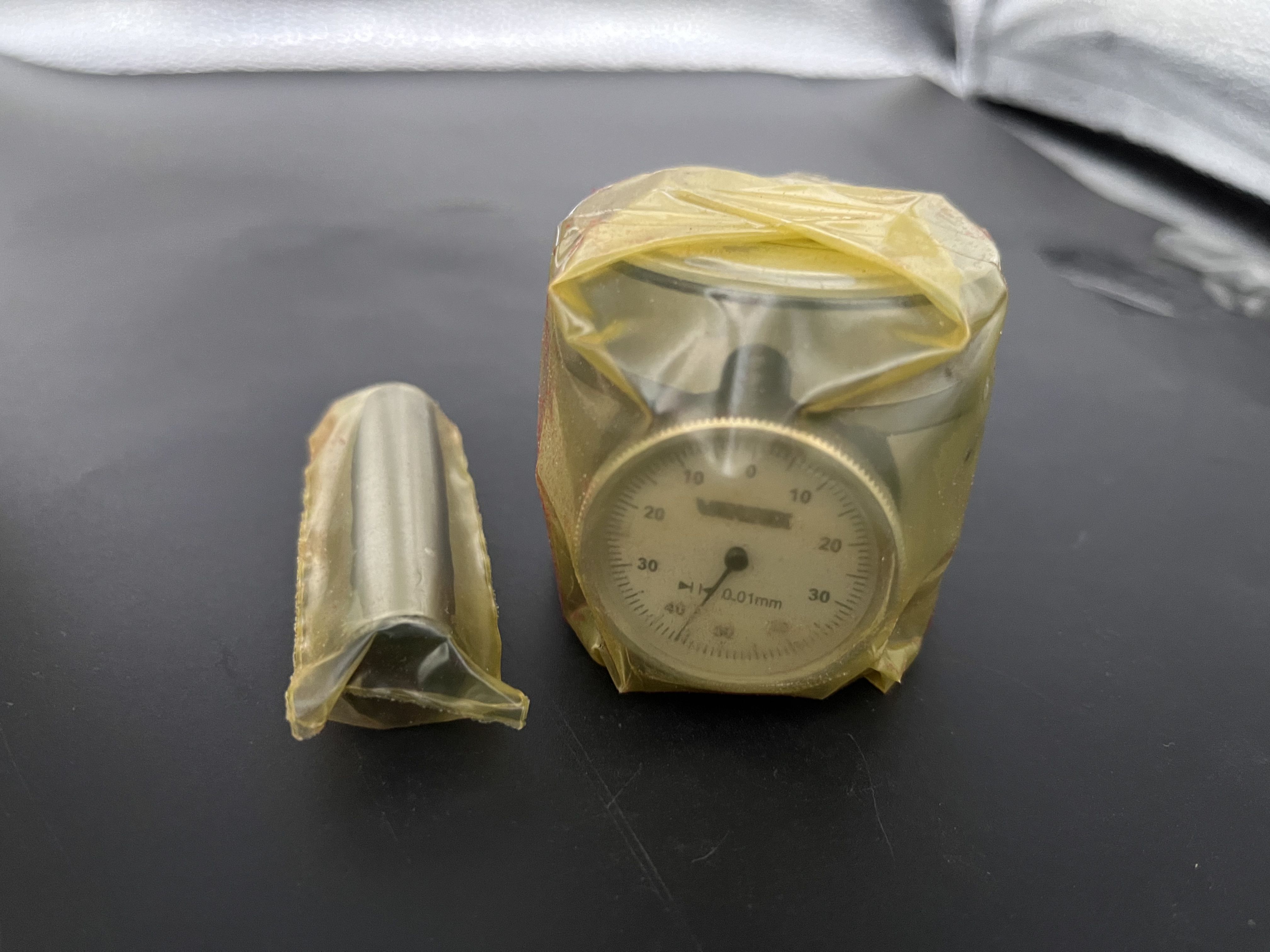
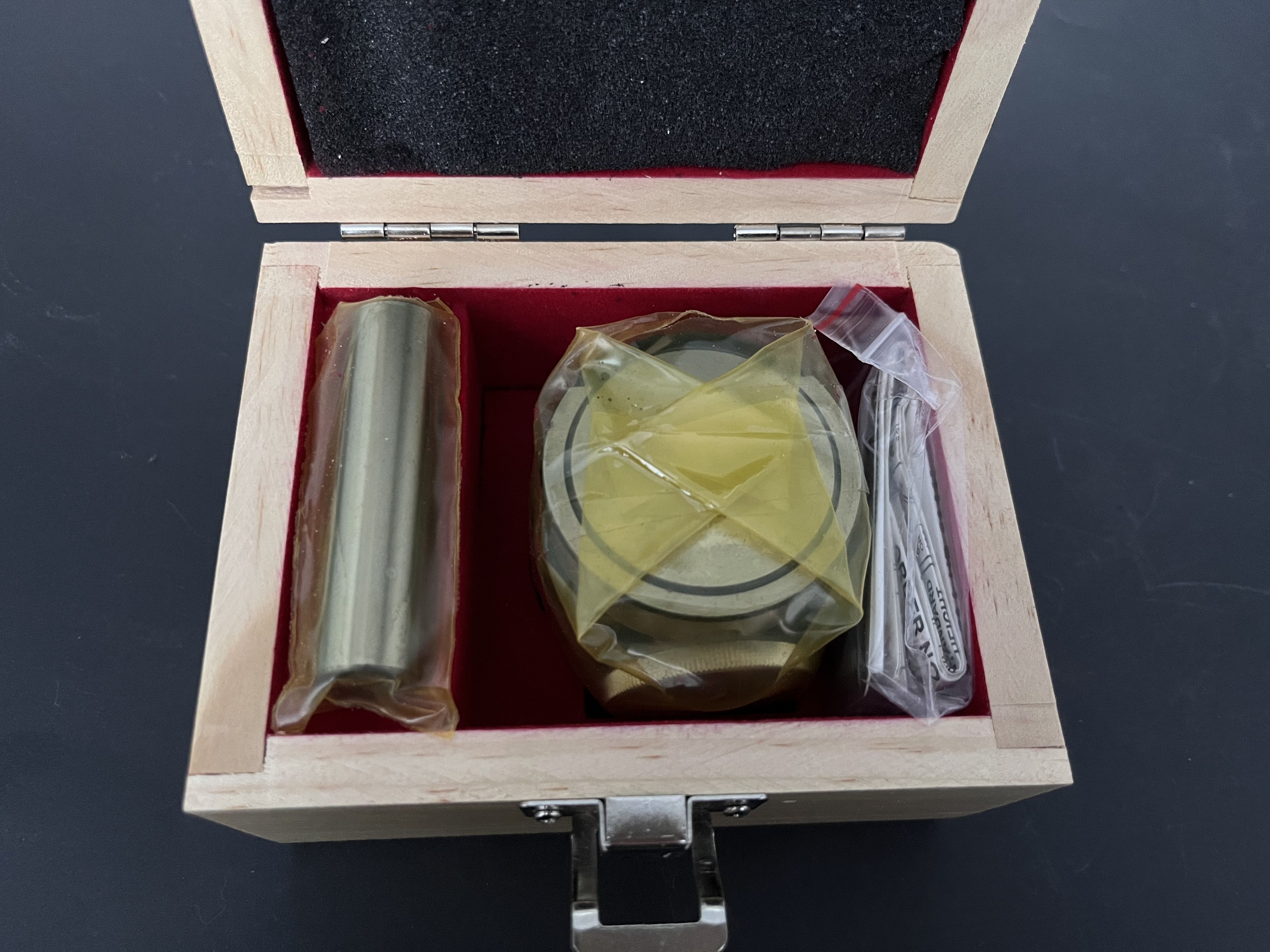

ભાગ ૧
વર્કપીસ ઓવરકટ:

કારણ:
૧) કટર ઉછાળવા માટે, સાધન પૂરતું મજબૂત નથી અને ખૂબ લાંબુ અથવા ખૂબ નાનું છે, જેના કારણે સાધન ઉછળે છે.
૨) ઓપરેટર દ્વારા અયોગ્ય કામગીરી.
૩) અસમાન કટીંગ ભથ્થું (ઉદાહરણ તરીકે: વક્ર સપાટીની બાજુએ ૦.૫ અને તળિયે ૦.૧૫ છોડો) ૪) અયોગ્ય કટીંગ પરિમાણો (ઉદાહરણ તરીકે: સહિષ્ણુતા ખૂબ મોટી છે, SF સેટિંગ ખૂબ ઝડપી છે, વગેરે)
સુધારો:
૧) કટર સિદ્ધાંતનો ઉપયોગ કરો: તે મોટું હોઈ શકે છે પણ નાનું નહીં, તે ટૂંકું હોઈ શકે છે પણ લાંબુ નહીં.
૨) ખૂણાની સફાઈ પ્રક્રિયા ઉમેરો, અને શક્ય તેટલું માર્જિન સમાન રાખવાનો પ્રયાસ કરો (બાજુ અને નીચેનો માર્જિન સુસંગત હોવો જોઈએ).
૩) કટીંગ પરિમાણોને વાજબી રીતે ગોઠવો અને ખૂણાઓને મોટા માર્જિન સાથે ગોળાકાર કરો.
૪) મશીન ટૂલના SF ફંક્શનનો ઉપયોગ કરીને, ઓપરેટર મશીન ટૂલની શ્રેષ્ઠ કટીંગ અસર પ્રાપ્ત કરવા માટે ઝડપને ફાઇન-ટ્યુન કરી શકે છે.

ભાગ ૨
ટૂલ સેટિંગ સમસ્યા

કારણ:
૧) મેન્યુઅલી ઓપરેટ કરતી વખતે ઓપરેટર સચોટ નથી.
૨) સાધન ખોટી રીતે ક્લેમ્પ્ડ છે.
૩) ફ્લાઇંગ કટર પરનો બ્લેડ ખોટો છે (ફ્લાઇંગ કટરમાં જ ચોક્કસ ભૂલો છે).
૪) આર કટર, ફ્લેટ કટર અને ફ્લાઈંગ કટર વચ્ચે ભૂલ છે.
સુધારો:
૧) મેન્યુઅલ કામગીરી વારંવાર કાળજીપૂર્વક તપાસવી જોઈએ, અને સાધન શક્ય તેટલું એક જ બિંદુ પર સેટ કરવું જોઈએ.
૨) ટૂલ ઇન્સ્ટોલ કરતી વખતે, તેને એર ગનથી ફૂંકીને સાફ કરો અથવા ચીંથરાથી સાફ કરો.
૩) જ્યારે ફ્લાઇંગ કટર પરના બ્લેડને ટૂલ હોલ્ડર પર માપવાની જરૂર હોય અને નીચેની સપાટીને પોલિશ કરવામાં આવે, ત્યારે બ્લેડનો ઉપયોગ કરી શકાય છે.
૪) એક અલગ ટૂલ સેટિંગ પ્રક્રિયા આર કટર, ફ્લેટ કટર અને ફ્લાઈંગ કટર વચ્ચેની ભૂલો ટાળી શકે છે.

ભાગ ૩
કોલાઈડર-પ્રોગ્રામિંગ

કારણ:
૧) સલામતી ઊંચાઈ પૂરતી નથી અથવા સેટ નથી (ઝડપી ફીડ G00 દરમિયાન કટર અથવા ચક વર્કપીસને અથડાવે છે).
૨) પ્રોગ્રામ યાદીમાંનું ટૂલ અને વાસ્તવિક પ્રોગ્રામ ટૂલ ખોટી રીતે લખાયેલ છે.
૩) પ્રોગ્રામ શીટ પર ટૂલની લંબાઈ (બ્લેડની લંબાઈ) અને વાસ્તવિક પ્રોસેસિંગ ઊંડાઈ ખોટી રીતે લખેલી છે.
૪) પ્રોગ્રામ શીટ પર ઊંડાઈ Z-અક્ષ ફેચ અને વાસ્તવિક Z-અક્ષ ફેચ ખોટી રીતે લખાયેલ છે.
૫) પ્રોગ્રામિંગ દરમિયાન કોઓર્ડિનેટ્સ ખોટી રીતે સેટ કરવામાં આવે છે.
સુધારો:
૧) વર્કપીસની ઊંચાઈ સચોટ રીતે માપો અને ખાતરી કરો કે સલામત ઊંચાઈ વર્કપીસથી ઉપર છે.
૨) પ્રોગ્રામ સૂચિ પરના સાધનો વાસ્તવિક પ્રોગ્રામ સાધનો સાથે સુસંગત હોવા જોઈએ (ઓટોમેટિક પ્રોગ્રામ સૂચિનો ઉપયોગ કરવાનો પ્રયાસ કરો અથવા પ્રોગ્રામ સૂચિ જનરેટ કરવા માટે ચિત્રોનો ઉપયોગ કરો).
૩) વર્કપીસ પર પ્રોસેસિંગની વાસ્તવિક ઊંડાઈ માપો, અને પ્રોગ્રામ શીટ પર ટૂલની લંબાઈ અને બ્લેડની લંબાઈ સ્પષ્ટ રીતે લખો (સામાન્ય રીતે ટૂલ ક્લેમ્પની લંબાઈ વર્કપીસ કરતા 2-3MM વધારે હોય છે, અને બ્લેડની લંબાઈ 0.5-1.0MM હોય છે).
૪) વર્કપીસ પર વાસ્તવિક Z-અક્ષ નંબર લો અને તેને પ્રોગ્રામ શીટ પર સ્પષ્ટ રીતે લખો. (આ કામગીરી સામાન્ય રીતે મેન્યુઅલી લખવામાં આવે છે અને તેને વારંવાર તપાસવાની જરૂર છે).

ભાગ ૪
કોલાઈડર-ઓપરેટર

કારણ:
૧) ડેપ્થ Z અક્ષ ટૂલ સેટિંગ ભૂલ·.
૨) પોઈન્ટની સંખ્યા હિટ થઈ છે અને કામગીરી ખોટી છે (જેમ કે: ફીડ ત્રિજ્યા વિના એકપક્ષીય ફેચિંગ, વગેરે).
૩) ખોટા ટૂલનો ઉપયોગ કરો (ઉદાહરણ તરીકે: પ્રોસેસિંગ માટે D10 ટૂલ સાથે D4 ટૂલનો ઉપયોગ કરો).
૪) પ્રોગ્રામ ખોટો પડ્યો (ઉદાહરણ તરીકે: A7.NC A9.NC પર ગયો).
૫) મેન્યુઅલ ઓપરેશન દરમિયાન હેન્ડવ્હીલ ખોટી દિશામાં ફરે છે.
૬) મેન્યુઅલ રેપિડ ટ્રાવર્સ દરમિયાન ખોટી દિશામાં દબાવો (ઉદાહરણ તરીકે: -X +X દબાવો).
સુધારો:
૧) ડીપ Z-એક્સિસ ટૂલ સેટિંગ કરતી વખતે, તમારે ટૂલ ક્યાં સેટ થઈ રહ્યું છે તેના પર ધ્યાન આપવું જોઈએ. (નીચલી સપાટી, ટોચની સપાટી, વિશ્લેષણ સપાટી, વગેરે).
૨) પૂર્ણ થયા પછી વારંવાર હિટ અને કામગીરીની સંખ્યા તપાસો.
૩) ટૂલ ઇન્સ્ટોલ કરતી વખતે, તેને ઇન્સ્ટોલ કરતા પહેલા પ્રોગ્રામ શીટ અને પ્રોગ્રામ સાથે વારંવાર તપાસો.
૪) કાર્યક્રમનું એક પછી એક ક્રમમાં પાલન કરવું આવશ્યક છે.
૫) મેન્યુઅલ ઓપરેશનનો ઉપયોગ કરતી વખતે, ઓપરેટરે પોતે મશીન ટૂલ ચલાવવામાં પોતાની કુશળતા વધારવી જોઈએ.
૬) જ્યારે મેન્યુઅલી ઝડપથી ખસેડો છો, ત્યારે તમે ખસેડતા પહેલા Z-અક્ષને વર્કપીસ પર ઉંચો કરી શકો છો.

ભાગ ૫
સપાટીની ચોકસાઈ

કારણ:
૧) કટીંગ પરિમાણો ગેરવાજબી છે અને વર્કપીસની સપાટી ખરબચડી છે.
૨) ઓજારની કટીંગ ધાર તીક્ષ્ણ નથી.
૩) ટૂલ ક્લેમ્પિંગ ખૂબ લાંબુ છે અને બ્લેડ ક્લિયરન્સ ખૂબ લાંબુ છે.
૪) ચીપ દૂર કરવી, હવા ફૂંકવી અને તેલ ફ્લશ કરવું સારું નથી.
૫) પ્રોગ્રામિંગ ટૂલ ફીડિંગ પદ્ધતિ (તમે ડાઉન મિલિંગનો વિચાર કરવાનો પ્રયાસ કરી શકો છો).
૬) વર્કપીસમાં ગડબડ છે.
સુધારો:
૧) કટીંગ પરિમાણો, સહિષ્ણુતા, ભથ્થાં, ગતિ અને ફીડ સેટિંગ્સ વાજબી હોવા જોઈએ.
૨) આ સાધન માટે ઓપરેટરને સમય સમય પર તેને તપાસવા અને બદલવાની જરૂર પડે છે.
૩) ટૂલને ક્લેમ્પ કરતી વખતે, ઓપરેટરે ક્લેમ્પ શક્ય તેટલો ટૂંકો રાખવો જરૂરી છે, અને બ્લેડ હવાથી બચવા માટે ખૂબ લાંબો ન હોવો જોઈએ.
૪) ફ્લેટ છરીઓ, આર છરીઓ અને રાઉન્ડ નોઝ છરીઓ વડે ડાઉનકટીંગ માટે, ઝડપ અને ફીડ સેટિંગ્સ વાજબી હોવી જોઈએ.
૫) વર્કપીસમાં બર હોય છે: તે આપણા મશીન ટૂલ, ટૂલ અને ટૂલ ફીડિંગ પદ્ધતિ સાથે સીધો સંબંધિત છે, તેથી આપણે મશીન ટૂલની કામગીરીને સમજવાની અને બર વડે કિનારીઓ ભરવાની જરૂર છે.

ભાગ ૬
ચીપિંગ એજ

૧) ખૂબ ઝડપથી ખોરાક આપો - યોગ્ય ફીડ ગતિ ધીમી કરો.
૨) કાપવાની શરૂઆતમાં ફીડ ખૂબ ઝડપી હોય છે - કાપવાની શરૂઆતમાં ફીડની ગતિ ધીમી કરો.
૩) ક્લેમ્પ લૂઝ (ટૂલ) - ક્લેમ્પ.
૪) ક્લેમ્પ લૂઝ (વર્કપીસ) - ક્લેમ્પ.
૫) અપૂરતી કઠોરતા (સાધન) - સૌથી ટૂંકા સાધનનો ઉપયોગ કરો, હેન્ડલને વધુ ઊંડે ક્લેમ્પ કરો અને મિલિંગ કરવાનો પ્રયાસ કરો.
૬) ટૂલની કટીંગ ધાર ખૂબ જ તીક્ષ્ણ છે - નાજુક કટીંગ ધારનો કોણ, પ્રાથમિક ધાર બદલો.
૭) મશીન ટૂલ અને ટૂલ હોલ્ડર પૂરતા કઠોર નથી - સારી કઠોરતાવાળા મશીન ટૂલ અને ટૂલ હોલ્ડરનો ઉપયોગ કરો.

ભાગ ૭
ઘસારો

૧) મશીનની ગતિ ખૂબ ઝડપી છે - ધીમી કરો અને પૂરતું શીતક ઉમેરો.
૨) કઠણ સામગ્રી - અદ્યતન કટીંગ ટૂલ્સ અને ટૂલ મટિરિયલ્સનો ઉપયોગ કરો, અને સપાટીની સારવાર પદ્ધતિઓમાં વધારો કરો.
૩) ચિપ એડહેસન - ફીડ સ્પીડ, ચિપનું કદ બદલો અથવા ચિપ્સ સાફ કરવા માટે કૂલિંગ ઓઇલ અથવા એર ગનનો ઉપયોગ કરો.
૪) ફીડ સ્પીડ અયોગ્ય છે (ખૂબ ઓછી) - ફીડ સ્પીડ વધારો અને ડાઉન મિલિંગનો પ્રયાસ કરો.
૫) કટીંગ એંગલ અયોગ્ય છે--તેને યોગ્ય કટીંગ એંગલમાં બદલો.
૬) ટૂલનો પ્રાથમિક રાહત કોણ ખૂબ નાનો છે - તેને મોટા રાહત કોણમાં બદલો.

ભાગ ૮
વાઇબ્રેશન પેટર્ન

૧) ફીડ અને કટીંગ સ્પીડ ખૂબ ઝડપી છે--ફીડ અને કટીંગ સ્પીડ સુધારો
૨) અપૂરતી કઠોરતા (મશીન ટૂલ અને ટૂલ હોલ્ડર)- વધુ સારા મશીન ટૂલ્સ અને ટૂલ હોલ્ડર્સનો ઉપયોગ કરો અથવા કટીંગની સ્થિતિ બદલો.
૩) રાહત કોણ ખૂબ મોટો છે - તેને નાના રાહત કોણમાં બદલો અને ધાર પર પ્રક્રિયા કરો (ધારને એકવાર શાર્પ કરવા માટે વ્હેટસ્ટોનનો ઉપયોગ કરો)
૪) ક્લેમ્પ લૂઝ કરો--વર્કપીસને ક્લેમ્પ કરો
૫) ઝડપ અને ફીડની માત્રા ધ્યાનમાં લો
ઝડપ, ફીડ અને કટીંગ ઊંડાઈ એ ત્રણ પરિબળો વચ્ચેનો સંબંધ કટીંગ અસર નક્કી કરવામાં સૌથી મહત્વપૂર્ણ પરિબળ છે. અયોગ્ય ફીડ અને ઝડપ ઘણીવાર ઉત્પાદનમાં ઘટાડો, નબળી વર્કપીસ ગુણવત્તા અને ગંભીર ટૂલ નુકસાન તરફ દોરી જાય છે.
પોસ્ટ સમય: જાન્યુઆરી-03-2024