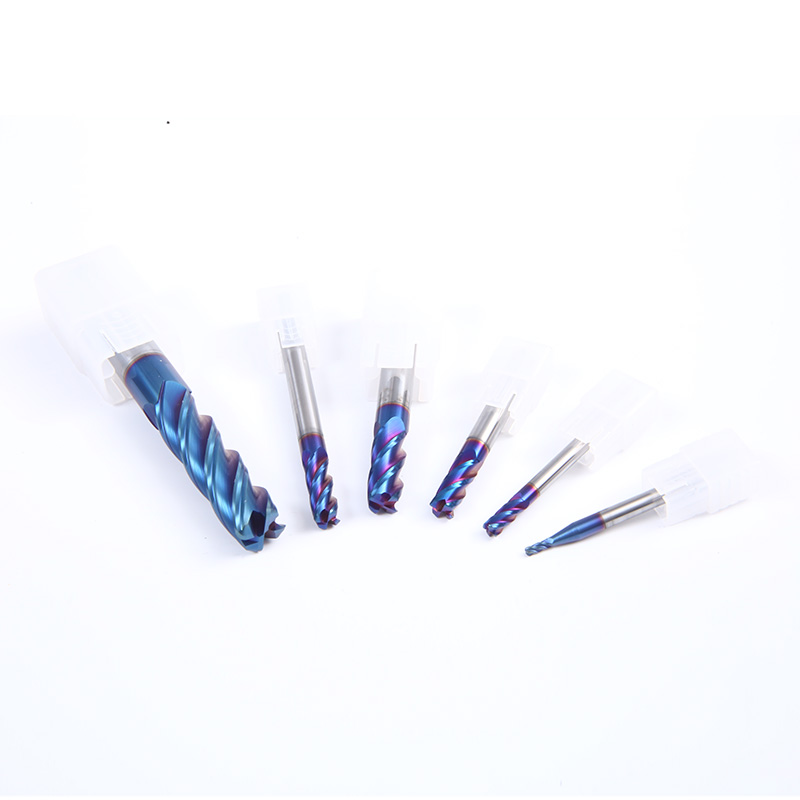

Parte 1

Cando se trata de mecanizado de precisión, ter as ferramentas adecuadas é esencial para obter resultados de alta calidade. Unha das ferramentas que gañou popularidade na industria do mecanizado é o muíño final HRC 65. Coñecida pola súa excepcional dureza e durabilidade, o muíño final HRC 65 converteuse nunha elección ideal para maquinistas e fabricantes que buscan conseguir operacións de corte precisas e eficientes.
O muíño final HRC 65 está deseñado para soportar as demandas de mecanizado de alta velocidade e é capaz de cortar unha ampla gama de materiais, incluíndo aceiros endurecidos, aceiro inoxidable e aliaxes exóticas. A súa alta cualificación de dureza de Rockwell de 65 convértea nunha elección ideal para aplicacións que requiren resistencia ao desgaste superior e rendemento de corte.
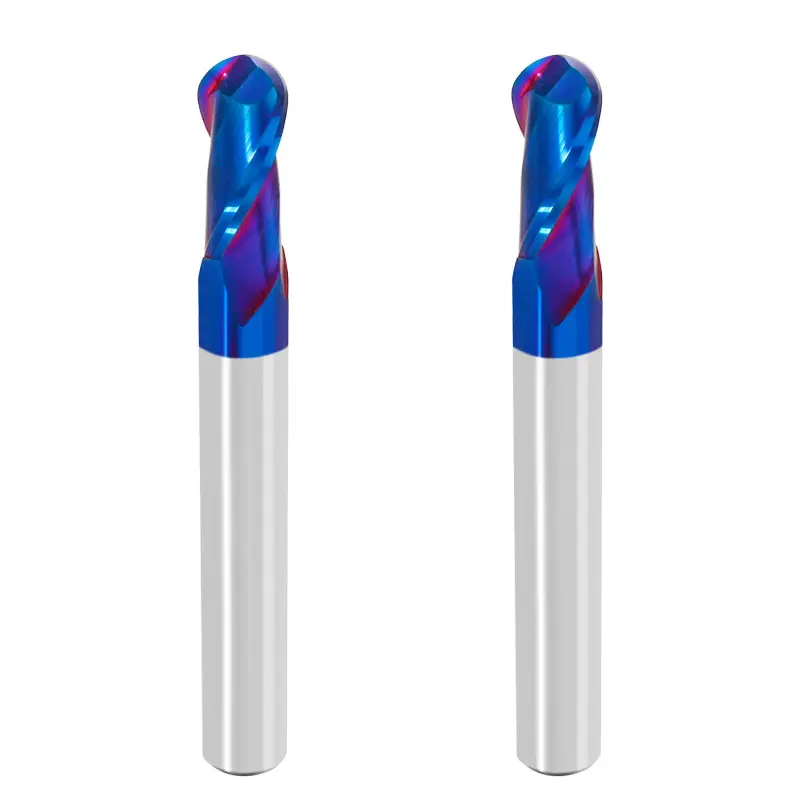

Parte 2

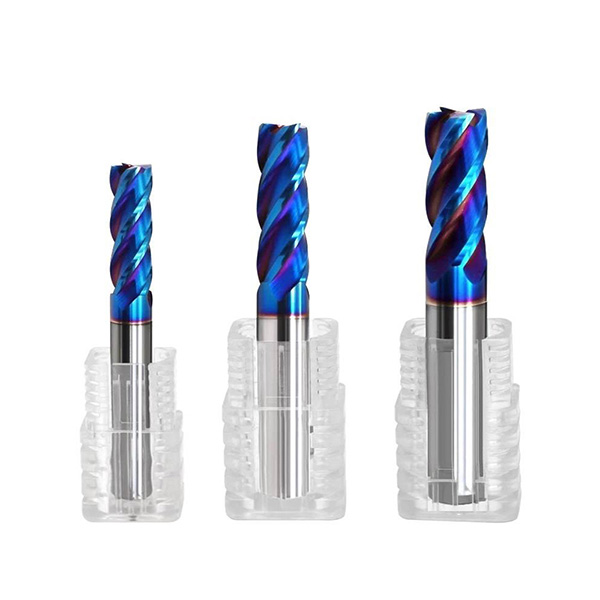
Unha marca que se fixo un nome na produción de MSK de alta calidade HRC 65 finais é MSK. Con reputación de excelencia e precisión, MSK converteuse nun nome de confianza na industria do mecanizado, ofrecendo unha serie de ferramentas de corte deseñadas para satisfacer as necesidades dos modernos procesos de fabricación.
O muíño final HRC 65 de MSK está deseñado para ofrecer un rendemento excepcional nunha variedade de aplicacións de mecanizado. Tanto se se trata de fresado, ranura ou perfilado, este muíño final está deseñado para proporcionar resultados consistentes e fiables, o que o converte nun activo valioso para maquinistas e fabricantes.

Parte 3

Unha das características clave do muíño final HRC 65 de MSK é a súa tecnoloxía avanzada de revestimento. O uso de revestimentos de alto rendemento como Tialn e Tisin aumenta a resistencia ao desgaste da ferramenta e a estabilidade térmica, permitindo unha vida prolongada e un mellor rendemento de corte. Isto significa que os maquinistas poden conseguir maiores velocidades e alimentos de corte, mantendo un excelente acabado superficial e precisión dimensional.
Ademais da súa tecnoloxía de revestimento superior, o muíño final HRC 65 de MSK está con precisión con materiais de carburo de alta calidade. Isto garante a capacidade da ferramenta para soportar as altas forzas de corte e temperaturas asociadas ás esixentes operacións de mecanizado, obtendo unha vida de ferramentas máis longa e reducidos custos de ferramentas para os fabricantes.
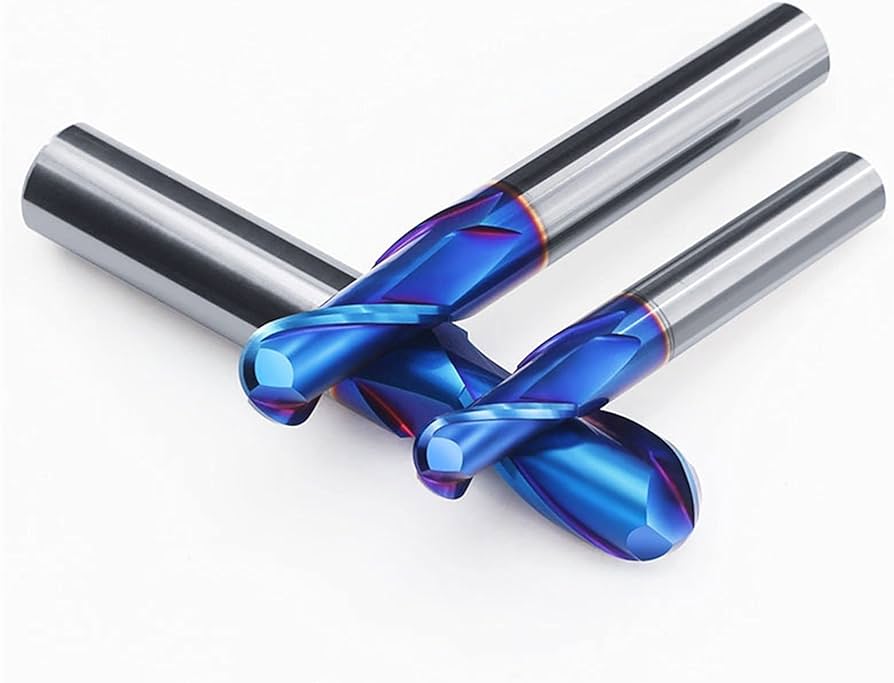

A xeometría do muíño final HRC 65 tamén está optimizada para unha evacuación de chip eficiente e reducidas forzas de corte, obtendo unha mellor estabilidade das ferramentas e unha vibración reducida durante o mecanizado. Isto non só leva a mellores acabados superficiais, senón que tamén contribúe á produtividade e á eficiencia global do proceso de mecanizado.
Ademais, o muíño final HRC 65 de MSK está dispoñible nunha variedade de configuracións, incluíndo opcións de extremo cadrado, nariz de bola e radio de esquina, permitindo aos maquinistas escoller a ferramenta adecuada para os seus requisitos específicos de aplicación. Esta versatilidade fai que o muíño final HRC 65 sexa un activo valioso para unha ampla gama de tarefas de mecanizado, desde asperacións ata as operacións de acabado.
Cando se trata de obter resultados de mecanizado precisos e precisos, o muíño final HRC 65 de MSK é unha ferramenta que destaca polo seu excepcional rendemento e fiabilidade. A súa combinación de alta dureza, tecnoloxía avanzada de revestimento e enxeñería de precisión convérteo nunha mellor opción para maquinistas e fabricantes que buscan optimizar os seus procesos de corte e obter resultados superiores.
En conclusión, o muíño final HRC 65 de MSK é un testamento dos avances na tecnoloxía de ferramentas de corte, ofrecendo aos maquinistas e aos fabricantes unha ferramenta que ofrece un rendemento, durabilidade e versatilidade excepcionais. Coa súa capacidade para soportar as demandas de mecanizado de alta velocidade e entregar resultados consistentes, o muíño final HRC 65 converteuse nunha ferramenta indispensable para aplicacións de mecanizado de precisión. A medida que a industria do mecanizado segue evolucionando, o muíño final de HRC 65 de MSK permanece na vangarda, proporcionando as solucións de punta necesarias para afrontar os retos da fabricación moderna.
Tempo post: 30-03 de abril