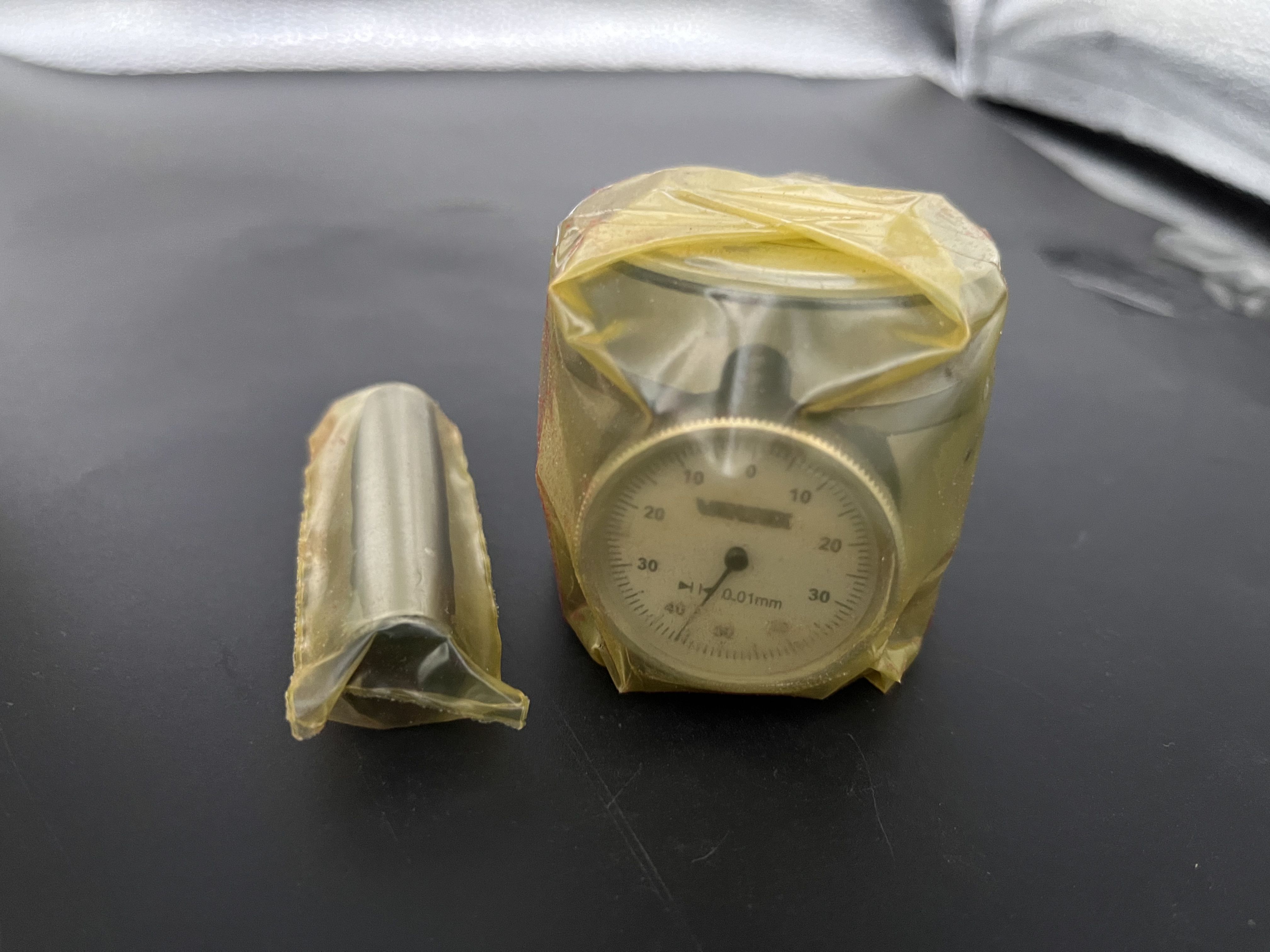
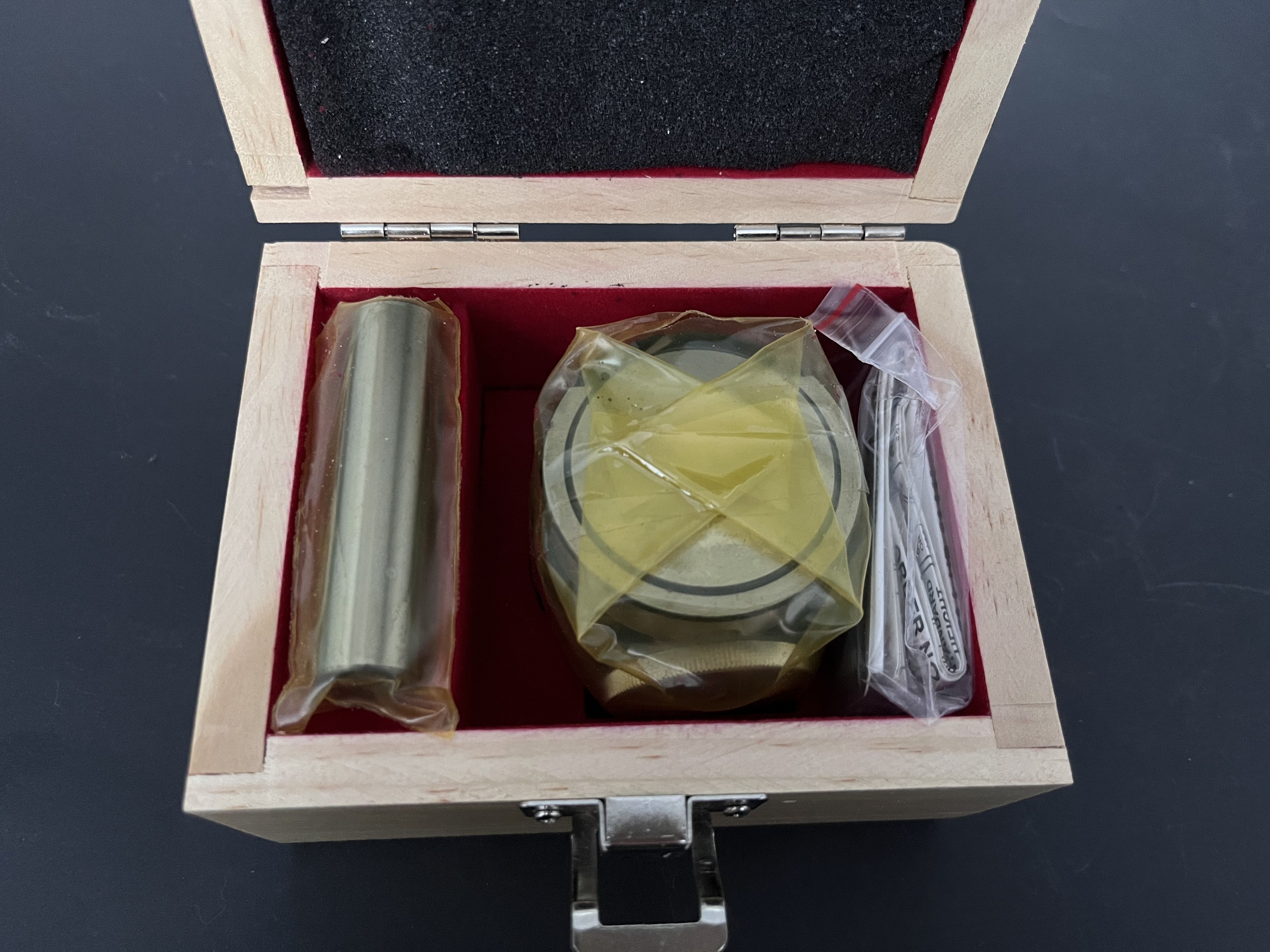

قسمت ۱
برش بیش از حد قطعه کار:

دلیل:
۱) برای پرش ابزار برش، ابزار به اندازه کافی محکم نیست و خیلی بلند یا خیلی کوچک است و باعث پرش ابزار میشود.
۲) عملکرد نادرست اپراتور.
۳) برش ناهموار (برای مثال: ۰.۵ در کنار سطح منحنی و ۰.۱۵ در پایین آن را در نظر بگیرید) ۴) پارامترهای برش نامناسب (برای مثال: تلرانس خیلی زیاد است، تنظیم SF خیلی سریع است و غیره)
بهبود:
۱) از اصل برش استفاده کنید: میتواند بزرگ باشد اما کوچک نباشد، میتواند کوتاه باشد اما بلند نباشد.
۲) روش تمیز کردن گوشهها را اضافه کنید و سعی کنید حاشیه را تا حد امکان یکنواخت نگه دارید (حاشیه کنار و پایین باید ثابت باشد).
۳) پارامترهای برش را به طور معقول تنظیم کنید و گوشهها را با حاشیههای بزرگ گرد کنید.
۴) با استفاده از عملکرد SF دستگاه، اپراتور میتواند سرعت را به طور دقیق تنظیم کند تا به بهترین اثر برش دستگاه دست یابد.

قسمت ۲
مشکل در تنظیم ابزار

دلیل:
۱) اپراتور هنگام کار دستی دقیق نیست.
۲) ابزار به طور نادرست گیره شده است.
۳) تیغهی روی کاتر پرنده نادرست است (خود کاتر پرنده خطاهای خاصی دارد).
۴) بین کاتر R، کاتر تخت و کاتر پرتابی خطایی وجود دارد.
بهبود:
۱) عملیات دستی باید به طور مکرر و با دقت بررسی شوند و ابزار تا حد امکان در یک نقطه ثابت قرار گیرد.
۲) هنگام نصب ابزار، آن را با تفنگ بادی تمیز کنید یا با یک دستمال آن را پاک کنید.
۳) هنگامی که تیغه روی دستگاه فرز پرنده نیاز به اندازهگیری روی نگهدارنده ابزار و صیقل دادن سطح زیرین دارد، میتوان از تیغه استفاده کرد.
۴) یک روش تنظیم ابزار جداگانه میتواند از خطاهای بین برش R، برش تخت و برش پرتابی جلوگیری کند.

قسمت ۳
برنامهنویسی برخورددهنده

دلیل:
۱) ارتفاع ایمنی کافی نیست یا تنظیم نشده است (برش یا سه نظام در حین تغذیه سریع G00 به قطعه کار برخورد میکند).
۲) ابزار موجود در فهرست برنامه و ابزار واقعی برنامه به اشتباه نوشته شدهاند.
۳) طول ابزار (طول تیغه) و عمق واقعی پردازش در برگه برنامه به اشتباه نوشته شده است.
۴) واکشی عمق محور Z و واکشی واقعی محور Z به اشتباه در برگه برنامه نوشته شدهاند.
۵) مختصات در حین برنامهریزی به اشتباه تنظیم شدهاند.
بهبود:
۱) ارتفاع قطعه کار را به طور دقیق اندازه گیری کنید و مطمئن شوید که ارتفاع ایمن بالای قطعه کار قرار دارد.
۲) ابزارهای موجود در فهرست برنامه باید با ابزارهای واقعی برنامه سازگار باشند (سعی کنید از فهرست خودکار برنامهها استفاده کنید یا از تصاویر برای تولید فهرست برنامهها استفاده کنید).
۳) عمق واقعی ماشینکاری روی قطعه کار را اندازه گیری کنید و طول و طول تیغه ابزار را به وضوح روی برگه برنامه بنویسید (به طور کلی طول گیره ابزار ۲-۳ میلی متر بالاتر از قطعه کار است و طول تیغه ۰.۵-۱.۰ میلی متر است).
۴) شماره واقعی محور Z را روی قطعه کار بردارید و آن را به طور واضح روی برگه برنامه بنویسید. (این عملیات عموماً به صورت دستی نوشته میشود و نیاز به بررسی مکرر دارد).

قسمت ۴
اپراتور برخورد دهنده

دلیل:
۱) خطای تنظیم ابزار محور Z در عمق.
۲) تعداد نقاط زده شده و عملیات اشتباه است (مانند: واکشی یکطرفه بدون شعاع تغذیه و غیره).
۳) از ابزار اشتباه استفاده کنید (برای مثال: از ابزار D4 به همراه ابزار D10 برای پردازش استفاده کنید).
۴) برنامه دچار مشکل شد (برای مثال: A7.NC به A9.NC رفت).
۵) در حین کار دستی، چرخ دستی در جهت اشتباه میچرخد.
۶) در حین حرکت سریع دستی، جهت اشتباه را فشار دهید (برای مثال: -X +X را فشار دهید).
بهبود:
۱) هنگام انجام تنظیمات عمیق ابزار محور Z، باید به محل تنظیم ابزار (سطح زیرین، سطح بالایی، سطح آنالیز و غیره) توجه کنید.
۲) تعداد بازدیدها و عملیات را پس از اتمام، مکرراً بررسی کنید.
۳) هنگام نصب ابزار، قبل از نصب، آن را بارها و بارها با برگه برنامه و برنامه بررسی کنید.
۴) برنامه باید یکی یکی و به ترتیب دنبال شود.
۵) هنگام استفاده از عملیات دستی، خود اپراتور باید مهارت خود را در کار با ابزار ماشینی بهبود بخشد.
۶) هنگام حرکت سریع دستی، میتوانید قبل از حرکت، ابتدا محور Z را تا قطعه کار بالا ببرید.

قسمت ۵
دقت سطح

دلیل:
۱) پارامترهای برش غیرمنطقی هستند و سطح قطعه کار ناهموار است.
۲) لبه برش ابزار تیز نیست.
۳) گیره ابزار خیلی طولانی است و فاصله تیغه از محور خیلی زیاد است.
۴) برادهبرداری، دمیدن هوا و شستشوی روغن خوب نیستند.
۵) روش تغذیه ابزار برنامهریزی (میتوانید فرزکاری رو به پایین را در نظر بگیرید).
۶) قطعه کار دارای پلیسه است.
بهبود:
۱) پارامترهای برش، تلرانسها، فواصل مجاز، سرعت و تنظیمات پیشروی باید منطقی باشند.
۲) این ابزار نیاز دارد که اپراتور هر از گاهی آن را بررسی و تعویض کند.
۳) هنگام بستن ابزار، اپراتور موظف است گیره را تا حد امکان کوتاه نگه دارد و تیغه نباید خیلی بلند باشد تا از ورود هوا جلوگیری شود.
۴) برای برش عمودی با چاقوهای تخت، چاقوهای R و چاقوهای دماغه گرد، تنظیمات سرعت و پیشروی باید معقول باشد.
۵) قطعه کار دارای پلیسه است: این موضوع ارتباط مستقیمی با ماشین ابزار، ابزار و روش تغذیه ابزار ما دارد، بنابراین باید عملکرد ماشین ابزار را درک کنیم و لبهها را با پلیسهها جبران کنیم.

قسمت ۶
لبه تراشیدن

۱) خیلی سریع غذا میدهید -- سرعت غذا دادن را کم کنید تا به سرعت مناسب برسید.
۲) سرعت پیشروی در ابتدای برش خیلی زیاد است -- سرعت پیشروی را در ابتدای برش کم کنید.
۳) گیره شل (ابزار) - گیره.
4) گیره شل (قطعه کار) - گیره.
۵) صلبیت ناکافی (ابزار) - از کوتاهترین ابزار مجاز استفاده کنید، دسته را عمیقتر ببندید و فرزکاری را امتحان کنید.
۶) لبه برش ابزار خیلی تیز است - زاویه لبه برش شکننده، لبه اولیه را تغییر دهید.
۷) ابزار ماشین و ابزارگیر به اندازه کافی سفت و محکم نیستند - از ابزار ماشین و ابزارگیر با سفتی خوب استفاده کنید.

قسمت ۷
ساییدگی و پارگی

۱) سرعت دستگاه خیلی زیاد است - سرعت را کم کنید و مایع خنک کننده کافی اضافه کنید.
۲) مواد سختشده - از ابزارهای برش و مواد ابزار پیشرفته استفاده کنید و روشهای عملیات سطحی را افزایش دهید.
۳) چسبندگی تراشه - سرعت پیشروی، اندازه تراشه را تغییر دهید یا از روغن خنککننده یا تفنگ بادی برای تمیز کردن تراشهها استفاده کنید.
۴) سرعت پیشروی نامناسب است (خیلی کم) - سرعت پیشروی را افزایش دهید و فرزکاری را آهستهتر امتحان کنید.
۵) زاویه برش نامناسب است -- آن را به زاویه برش مناسب تغییر دهید.
۶) زاویهی امداد اولیهی ابزار خیلی کوچک است - آن را به زاویهی امداد بزرگتری تغییر دهید.

قسمت ۸
الگوی ارتعاش

۱) سرعت پیشروی و برش خیلی زیاد است - سرعت پیشروی و برش را اصلاح کنید
۲) صلبیت ناکافی (ماشین ابزار و ابزارگیر) - از ماشین ابزار و ابزارگیرهای بهتر استفاده کنید یا شرایط برش را تغییر دهید
۳) زاویه برجستگی خیلی بزرگ است - آن را به زاویه برجستگی کوچکتری تغییر دهید و لبه را پردازش کنید (یک بار از سنگ تیزکن برای تیز کردن لبه استفاده کنید)
۴) گیره را شل کنید - قطعه کار را محکم بگیرید
۵) سرعت و میزان تغذیه را در نظر بگیرید
رابطه بین سه عامل سرعت، پیشروی و عمق برش مهمترین عامل در تعیین اثر برش است. پیشروی و سرعت نامناسب اغلب منجر به کاهش تولید، کیفیت پایین قطعه کار و آسیب شدید ابزار می شود.
زمان ارسال: ژانویه-03-2024