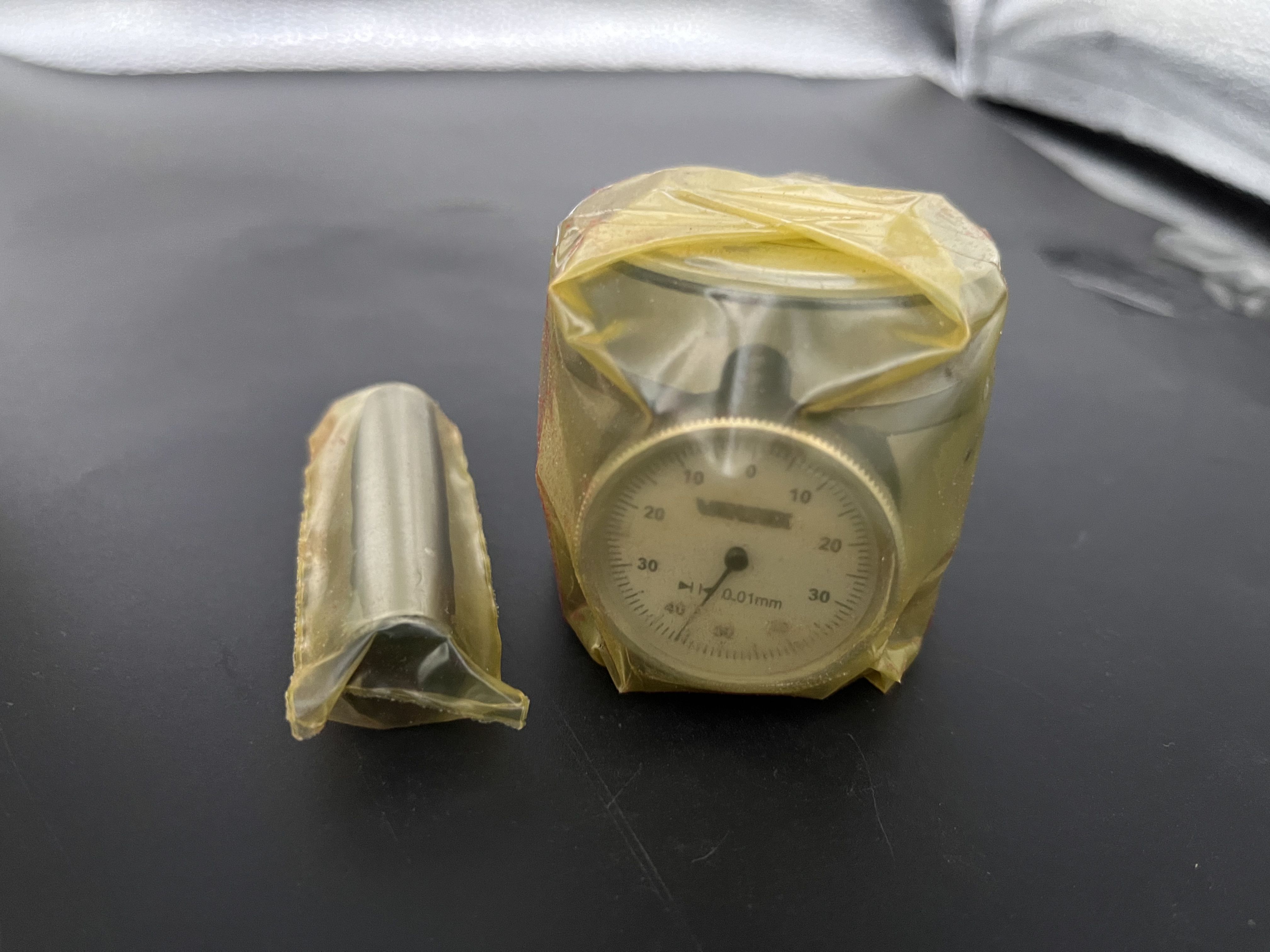
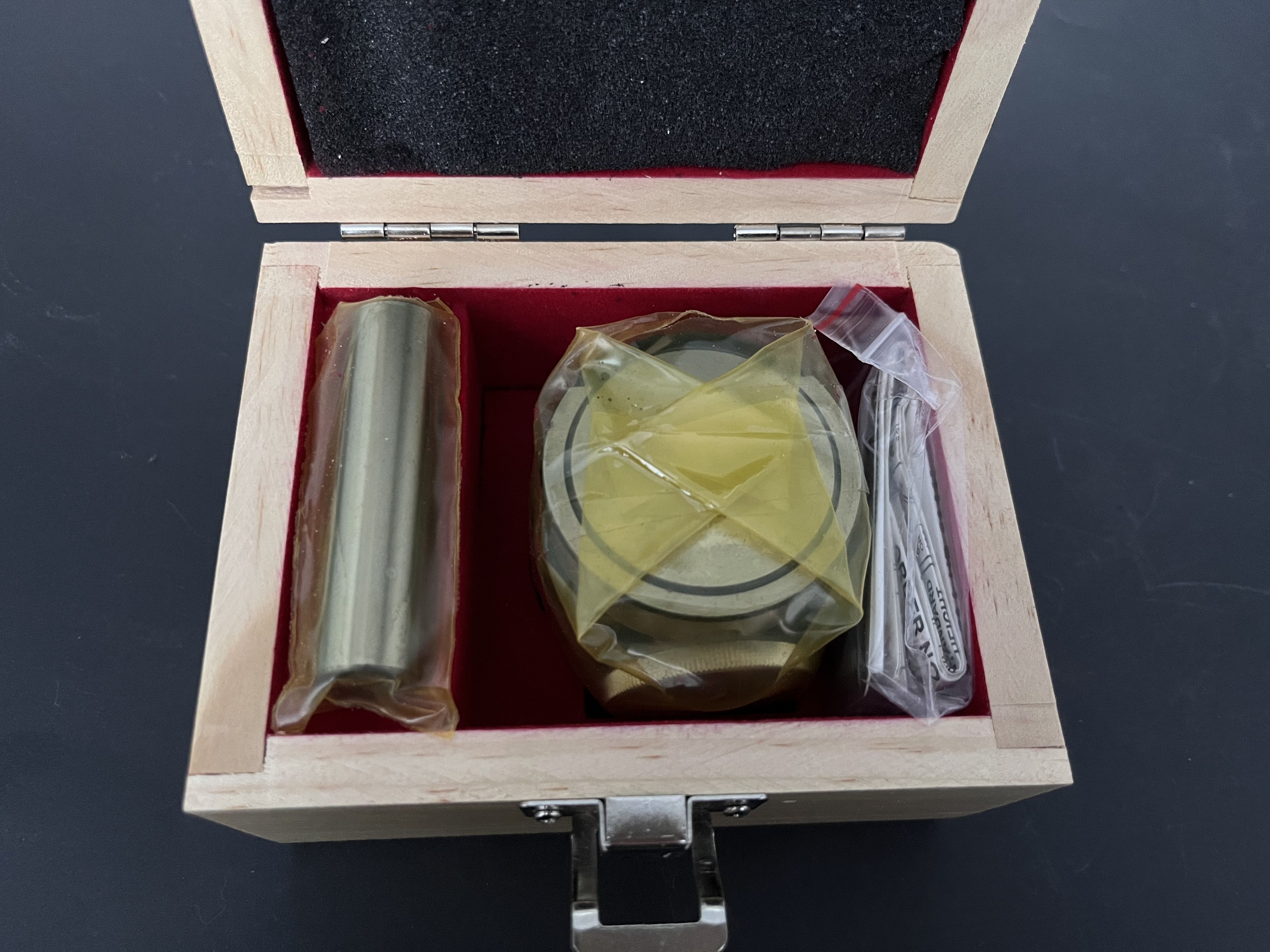

Teil 1
Werkstücküberschnitt:

Grund:
1) Das Werkzeug ist nicht stark genug und zu lang oder zu klein, sodass es zurückprallt.
2) Unsachgemäße Bedienung durch den Bediener.
3) Ungleichmäßige Schnittzugabe (zum Beispiel: 0,5 an der Seite der gekrümmten Oberfläche und 0,15 an der Unterseite lassen) 4) Ungeeignete Schnittparameter (zum Beispiel: Die Toleranz ist zu groß, die SF-Einstellung ist zu schnell usw.)
verbessern:
1) Wenden Sie das Cutter-Prinzip an: Es darf groß sein, aber nicht klein, es darf kurz sein, aber nicht lang.
2) Fügen Sie das Verfahren zur Eckenreinigung hinzu und versuchen Sie, den Rand so gleichmäßig wie möglich zu halten (der Rand an der Seite und am Boden sollte einheitlich sein).
3) Passen Sie die Schnittparameter sinnvoll an und runden Sie die Ecken mit großen Rändern ab.
4) Mithilfe der SF-Funktion der Werkzeugmaschine kann der Bediener die Geschwindigkeit feinabstimmen, um die beste Schneidwirkung der Werkzeugmaschine zu erzielen.

Teil 2
Problem bei der Werkzeugeinstellung

Grund:
1) Der Bediener ist bei manueller Bedienung nicht genau.
2) Das Werkzeug ist falsch eingespannt.
3) Die Klinge am fliegenden Messer ist falsch (das fliegende Messer selbst weist bestimmte Fehler auf).
4) Es liegt ein Fehler zwischen R-Fräser, Flachfräser und fliegendem Fräser vor.
verbessern:
1) Manuelle Vorgänge sollten wiederholt sorgfältig überprüft werden und das Werkzeug sollte möglichst immer an derselben Stelle eingestellt werden.
2) Blasen Sie das Werkzeug beim Einbau mit einer Druckluftpistole sauber oder wischen Sie es mit einem Lappen sauber.
3) Wenn die Klinge des fliegenden Fräsers am Werkzeughalter gemessen werden muss und die Unterseite poliert ist, kann eine Klinge verwendet werden.
4) Durch ein separates Werkzeugeinstellungsverfahren können Fehler zwischen R-Fräser, Flachfräser und fliegendem Fräser vermieden werden.

Teil 3
Collider-Programmierung

Grund:
1) Die Sicherheitshöhe ist nicht ausreichend oder nicht eingestellt (Fräser oder Spannfutter trifft beim Eilgang G00 auf das Werkstück).
2) Das Werkzeug in der Programmliste und das eigentliche Programmwerkzeug sind falsch geschrieben.
3) Die Werkzeuglänge (Schneidenlänge) und die tatsächliche Bearbeitungstiefe sind auf dem Programmblatt falsch angegeben.
4) Die Tiefe des Z-Achsen-Abrufs und der tatsächliche Z-Achsen-Abruf sind auf dem Programmblatt falsch angegeben.
5) Beim Programmieren wurden die Koordinaten falsch eingestellt.
verbessern:
1) Messen Sie die Höhe des Werkstücks genau und stellen Sie sicher, dass die sichere Höhe über dem Werkstück liegt.
2) Die Tools in der Programmliste müssen mit den tatsächlichen Programmtools übereinstimmen (versuchen Sie, eine automatische Programmliste zu verwenden oder Bilder zum Generieren der Programmliste zu verwenden).
3) Messen Sie die tatsächliche Bearbeitungstiefe des Werkstücks und notieren Sie die Länge und Klingenlänge des Werkzeugs deutlich auf dem Programmblatt (im Allgemeinen ist die Werkzeugklemmlänge 2–3 mm höher als das Werkstück und die Klingenlänge beträgt 0,5–1,0 mm).
4) Notieren Sie die tatsächliche Z-Achsennummer auf dem Werkstück und schreiben Sie sie deutlich auf das Programmblatt. (Dieser Vorgang wird im Allgemeinen manuell geschrieben und muss wiederholt überprüft werden.)

Teil 4
Collider-Operator

Grund:
1) Fehler bei der Werkzeugeinstellung für die Tiefe der Z-Achse.
2) Die Punktzahl wird erreicht und die Bedienung ist falsch (zB: einseitiges Holen ohne Vorschubradius, etc.).
3) Verwenden Sie das falsche Werkzeug (zum Beispiel: Verwenden Sie zur Verarbeitung das D4-Werkzeug mit dem D10-Werkzeug).
4) Das Programm ist fehlerhaft (Beispiel: A7.NC wurde zu A9.NC).
5) Das Handrad dreht sich bei manueller Bedienung in die falsche Richtung.
6) Beim manuellen Eilgang die falsche Richtung drücken (Beispiel: -X drücken +X).
verbessern:
1) Wenn Sie eine tiefe Z-Achsen-Werkzeugeinstellung durchführen, müssen Sie darauf achten, wo das Werkzeug eingestellt wird. (Unterseite, Oberseite, Analyseoberfläche usw.).
2) Überprüfen Sie die Anzahl der Treffer und Operationen nach Abschluss wiederholt.
3) Überprüfen Sie das Werkzeug bei der Installation vor der Installation wiederholt anhand des Programmblatts und des Programms.
4) Das Programm muss der Reihe nach Schritt für Schritt befolgt werden.
5) Bei manueller Bedienung muss der Bediener seine Kenntnisse in der Bedienung der Werkzeugmaschine selbst verbessern.
6) Bei schnellen manuellen Bewegungen können Sie die Z-Achse vor der Bewegung zunächst zum Werkstück anheben.

Teil 5
Oberflächengenauigkeit

Grund:
1) Die Schnittparameter sind unangemessen und die Werkstückoberfläche ist rau.
2) Die Schneide des Werkzeugs ist nicht scharf.
3) Die Werkzeugklemmung ist zu lang und der Klingenabstand ist zu groß.
4) Spanabfuhr, Luftblasen und Ölspülen sind nicht gut.
5) Programmieren der Werkzeugvorschubmethode (Sie können versuchen, das Gleichlauffräsen in Betracht zu ziehen).
6) Das Werkstück weist Grate auf.
verbessern:
1) Schnittparameter, Toleranzen, Zugaben, Geschwindigkeits- und Vorschubeinstellungen müssen angemessen sein.
2) Das Werkzeug muss vom Bediener von Zeit zu Zeit überprüft und ausgetauscht werden.
3) Beim Einspannen des Werkzeugs muss der Bediener die Klemme so kurz wie möglich halten und die Klinge sollte nicht zu lang sein, um Luft zu vermeiden.
4) Beim Gleichlaufschneiden mit Flachmessern, R-Messern und Rundmessern müssen die Geschwindigkeits- und Vorschubeinstellungen angemessen sein.
5) Das Werkstück weist Grate auf: Dies hängt direkt mit unserer Werkzeugmaschine, unserem Werkzeug und der Werkzeugzufuhrmethode zusammen. Daher müssen wir die Leistung der Werkzeugmaschine verstehen und die Kanten mit Graten ausgleichen.

Teil 6
Abplatzkante

1) Zu schneller Vorschub – auf eine geeignete Vorschubgeschwindigkeit verlangsamen.
2) Der Vorschub ist zu Beginn des Schnitts zu schnell. Verlangsamen Sie die Vorschubgeschwindigkeit zu Beginn des Schnitts.
3) Klemme gelöst (Werkzeug) - Klemme.
4) Klemme lösen (Werkstück) - Klemme.
5) Unzureichende Steifigkeit (Werkzeug) - Verwenden Sie das kürzeste zulässige Werkzeug, klemmen Sie den Griff tiefer ein und versuchen Sie es mit Fräsen.
6) Die Schneide des Werkzeugs ist zu scharf – ändern Sie den Winkel der empfindlichen Schneide, der Hauptschneide.
7) Die Werkzeugmaschine und der Werkzeughalter sind nicht steif genug – verwenden Sie eine Werkzeugmaschine und einen Werkzeughalter mit guter Steifigkeit.

Teil 7
Verschleiß

1) Die Maschinengeschwindigkeit ist zu hoch. Reduzieren Sie die Geschwindigkeit und fügen Sie ausreichend Kühlmittel hinzu.
2) Gehärtete Materialien – verwenden Sie fortschrittliche Schneidwerkzeuge und Werkzeugmaterialien und verbessern Sie die Methoden der Oberflächenbehandlung.
3) Spanhaftung – ändern Sie die Vorschubgeschwindigkeit, Spangröße oder verwenden Sie Kühlöl oder eine Druckluftpistole, um die Späne zu reinigen.
4) Die Vorschubgeschwindigkeit ist ungeeignet (zu niedrig) - erhöhen Sie die Vorschubgeschwindigkeit und versuchen Sie es mit Gegenlauffräsen.
5) Der Schnittwinkel ist ungeeignet. Ändern Sie ihn in einen geeigneten Schnittwinkel.
6) Der primäre Freiwinkel des Werkzeugs ist zu klein – ändern Sie ihn in einen größeren Freiwinkel.

Teil 8
Schwingungsmuster

1) Der Vorschub und die Schnittgeschwindigkeit sind zu hoch - korrigieren Sie den Vorschub und die Schnittgeschwindigkeit
2) Unzureichende Steifigkeit (Werkzeugmaschine und Werkzeughalter) – verwenden Sie bessere Werkzeugmaschinen und Werkzeughalter oder ändern Sie die Schnittbedingungen
3) Der Freiwinkel ist zu groß - ändern Sie ihn auf einen kleineren Freiwinkel und bearbeiten Sie die Kante (verwenden Sie einen Schleifstein, um die Kante einmal zu schärfen).
4) Klemme lösen - Werkstück festklemmen
5) Berücksichtigen Sie Geschwindigkeit und Vorschubmenge
Das Verhältnis der drei Faktoren Drehzahl, Vorschub und Schnitttiefe ist der wichtigste Faktor für die Schnittwirkung. Ungeeignete Vorschübe und Drehzahlen führen häufig zu Produktionseinbußen, schlechter Werkstückqualität und schweren Werkzeugschäden.
Beitragszeit: 03.01.2024