Hochwertiger Import M35 Gewindeformer für Fräsmaschinen
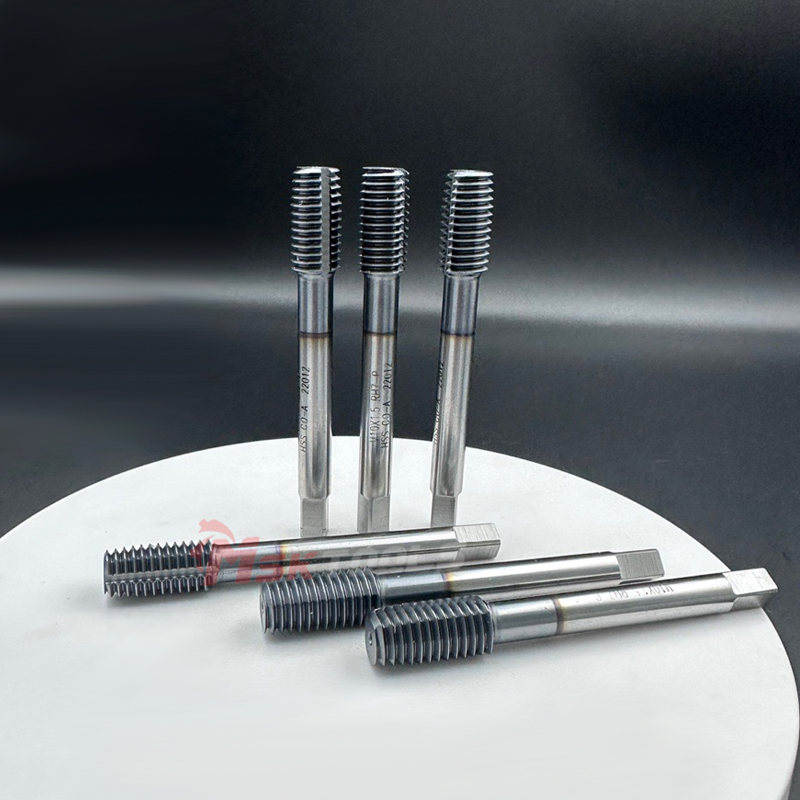
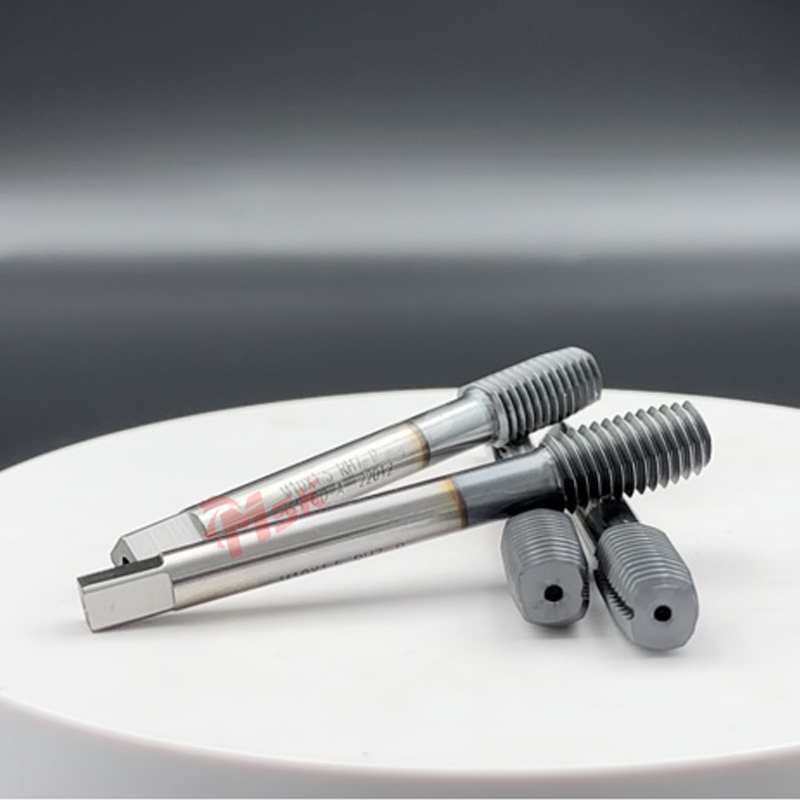
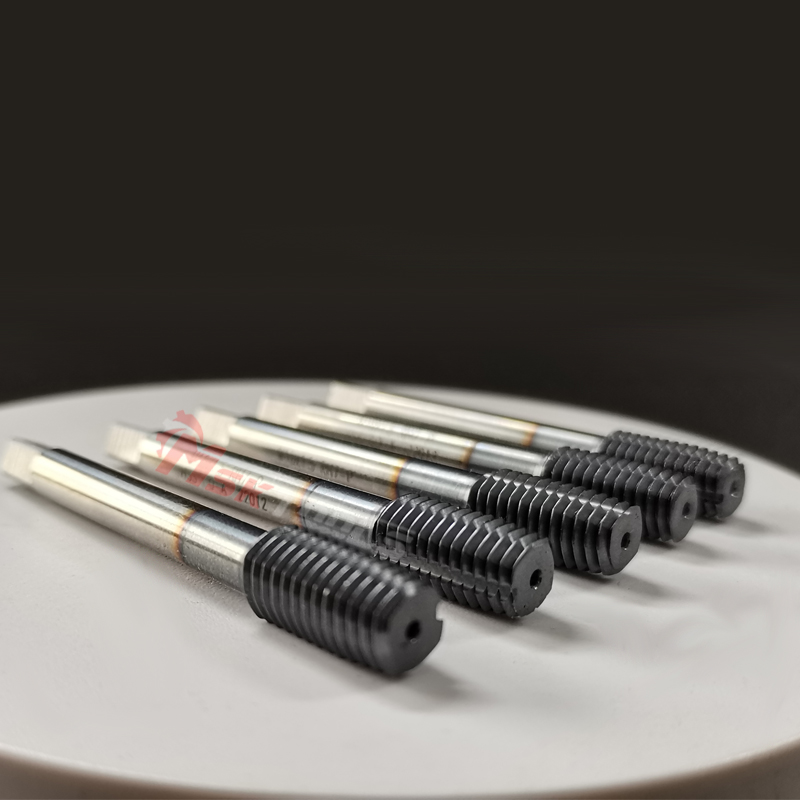
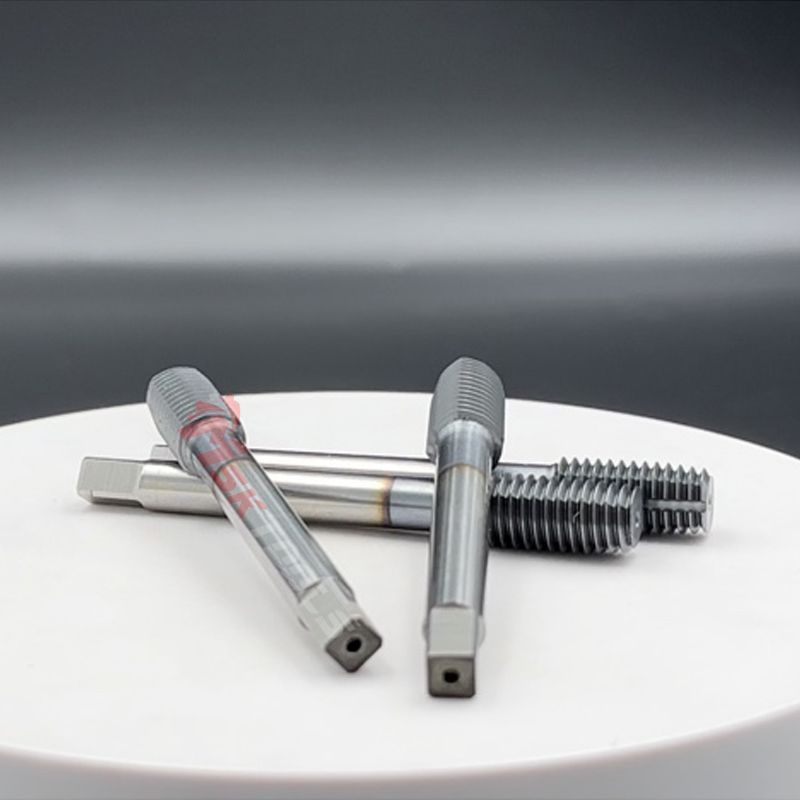
PRODUKTBESCHREIBUNG
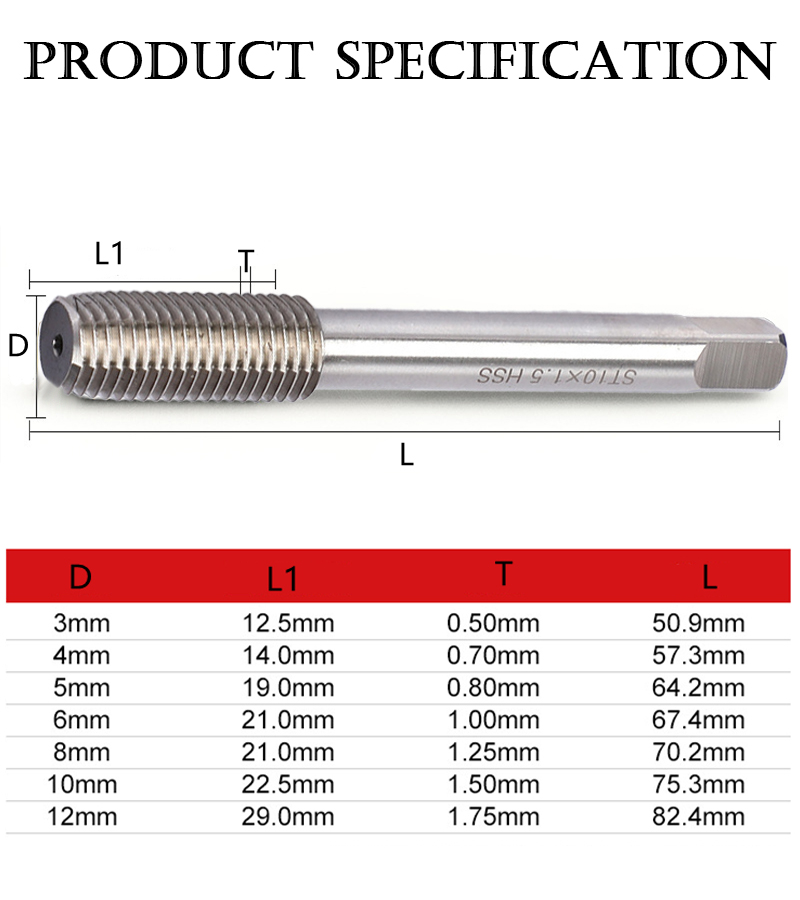
Marke | MSK | Beschichtung | Zinn |
Mindestbestellmenge | 3 Stück | Verwenden Sie Ausrüstung | CNC-Ausrüstung, Präzisionsbohrmaschine |
Material | M35 importieren | Haltertyp | Japanischer Standard |
VORTEIL
Titel: Verbesserung der Effizienz und Genauigkeit mit Gewindeformern
einführen:
In der heutigen schnelllebigen Fertigung sind Effizienz und Präzision entscheidend. Der Gewindeformer ist ein Werkzeug, das den Gewindeherstellungsprozess revolutioniert hat. Dieses innovative Werkzeug erhöht die Zuverlässigkeit und Haltbarkeit von Gewindeverbindungen im Vergleich zu herkömmlichen Methoden deutlich. In diesem Blogbeitrag erläutern wir die Vorteile des Gewindeformers und wie er Fertigungsabläufe vereinfachen kann.
1. Die Funktion verstehen:
Gewindeformer sind unverzichtbare Präzisionswerkzeuge in der Zerspanungsindustrie. Im Gegensatz zu herkömmlichen Gewindebohrern, die Gewinde schneiden, formen Gewindeformer das Material um und erzeugen so Gewinde mit außergewöhnlicher Präzision und Konsistenz. Durch kontrollierten Druck bewegt der Gewindeformer das Material, ohne Spannungskonzentrationen zu verursachen. Dieser Verformungsprozess stärkt nicht nur das Gewinde, sondern reduziert auch das Risiko von Rissen oder Schwachstellen im Material. Dadurch können sich Unternehmen auf die Widerstandsfähigkeit und Langlebigkeit von Gewindeverbindungen verlassen.
2. Wesentliche Vorteile:
Die Verwendung eines Gewindeformers bietet mehrere Vorteile, die ihn in vielen Anwendungen zur ersten Wahl machen. Neben der Erhöhung der Festigkeit und Haltbarkeit von Gewinden verringern diese Gewindebohrer das Risiko von Materialabrissen oder -beschädigungen. Die entstehenden Gewinde sind äußerst vibrations- und lösebeständig und somit zuverlässiger in kritischen Baugruppen. Dank des effizienten Verformungsprozesses können Anwender zudem eine höhere Produktivität erzielen und gleichzeitig Ausschuss und Nacharbeit minimieren. Gewindeformer sind zudem umweltfreundlich, da sie weniger Energie benötigen und weniger Späne produzieren als herkömmliche Gewindebohrverfahren.
3. Geeignete Anwendungen:
Gewindeformer werden in zahlreichen Branchen eingesetzt, darunter in der Automobilindustrie, der Luft- und Raumfahrt, im Sanitärbereich und in der Elektronik. Ihre Fähigkeit, Gewinde in verschiedenen Materialien wie Metallen, Kunststoffen und Verbundwerkstoffen zu formen, trägt zu ihrer Vielseitigkeit bei. Ob Gewinde in Aluminium-Motorblöcken, Edelstahlarmaturen oder Kunststoffgehäusekomponenten – Gewindeformer liefern gleichbleibende Ergebnisse. Ihre Kompatibilität mit verschiedenen Materialarten gewährleistet, dass Hersteller ihre Prozesse optimieren können, ohne Kompromisse bei Präzision oder Effizienz einzugehen.
4. Best Practices für beste Ergebnisse:
Um die Vorteile von Gewindeformern optimal zu nutzen, müssen die bewährten Verfahren der Branche befolgt werden. Entscheidend ist zunächst die Wahl der richtigen Gewindeformergeometrie für das Gewindematerial. Dies gewährleistet eine korrekte Verformung ohne übermäßige Krafteinwirkung und minimiert das Risiko von Werkzeugbruch oder Gewindedrehungen. Auch eine präzise Schmierung beim Gewindeschneiden trägt entscheidend zum Erreichen optimaler Ergebnisse bei. Darüber hinaus tragen ausreichende Maschinenstabilität und die Einhaltung der richtigen Schnittgeschwindigkeiten zur Erhöhung der Lebensdauer des Gewindebohrers und der Gesamteffizienz des Gewindeschneidens bei.
abschließend:
Gewindeformer haben die Fertigung revolutioniert und revolutioniert. Ihre Fähigkeit, starke, zuverlässige und präzise Gewinde zu erzeugen und gleichzeitig die Effizienz zu steigern, macht sie zu einem unverzichtbaren Werkzeug in unzähligen Anwendungen. Der Einsatz von Gewindeformern verbessert nicht nur die Qualität von Gewindeverbindungen, sondern steigert auch die Gesamtproduktivität der Bearbeitungsvorgänge. Durch den Einsatz dieser innovativen Technologie können Hersteller ihre führende Position in einem hart umkämpften Markt behaupten, strenge Qualitätsstandards einhalten und die Langlebigkeit von Gewindekomponenten gewährleisten.
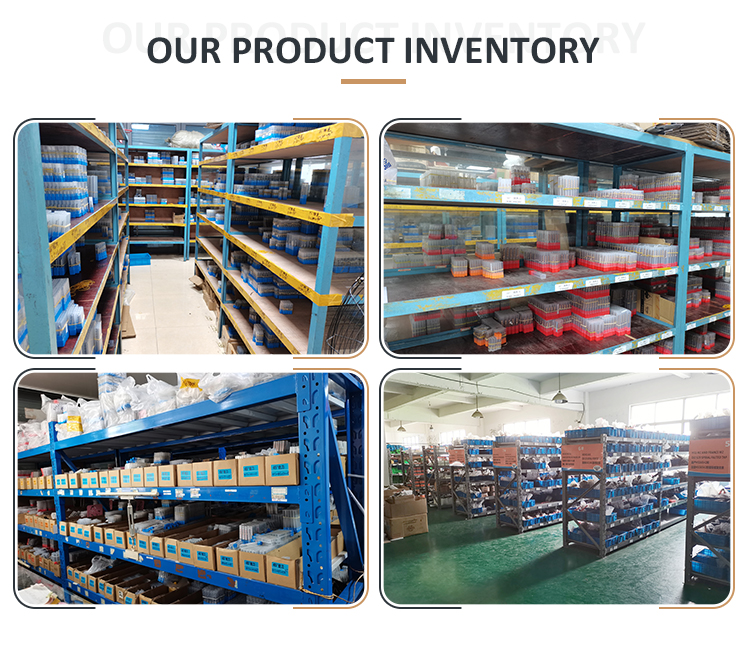
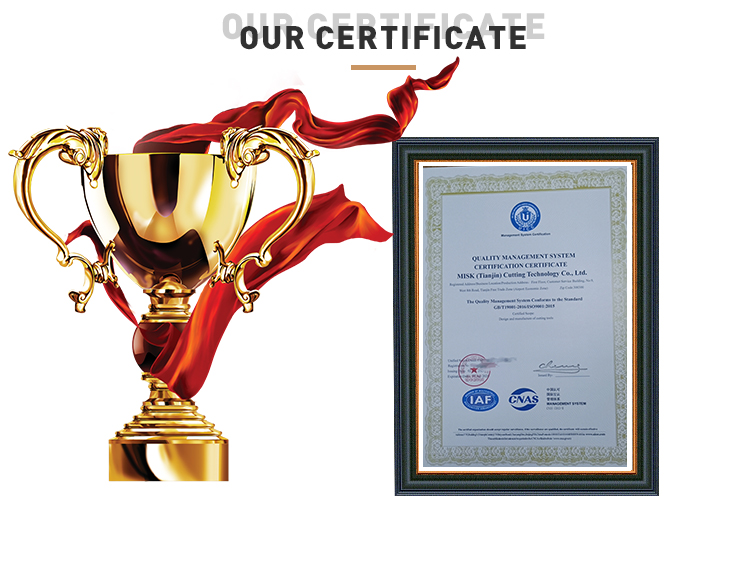